Top 3 Reasons for Hydraulic Hose Failure
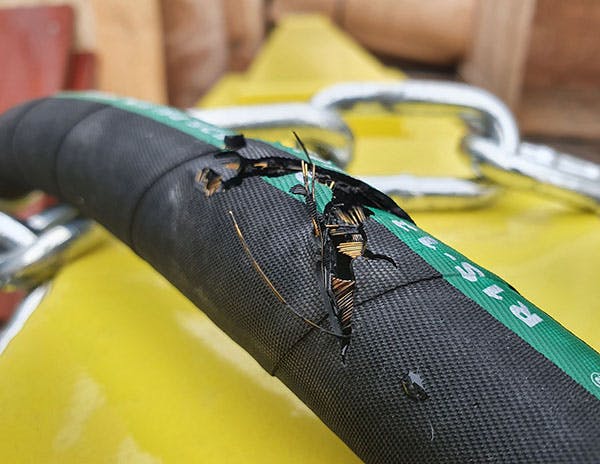
The top three reasons why hydraulic hoses fail are heat, abrasion, improper bend/erosion.
Just like pneumatics, hydraulic mechanisms are used throughout industrial applications. Hydraulic systems provide a safe and simple way to manipulate fluid properties to carry out linear, reciprocating, or circular motion in cranes, planes, forklifts, jacks, and even amusement park rides, giving high power with excellent control.
Most hydraulic systems don’t have many moving parts, but their hoses tend to wear out with time and result in unnecessary machine downtime. Here are some common reasons why hydraulic hoses fail.
Heat
Most hydraulic systems rely on an engine to drive a pump that builds pressure for the hydraulic circuit. The engine generates a lot of heat that is detrimental to hydraulic hoses running along with it if proper heat shielding is not done. The heat generated causes the internal rubber liner to melt, resulting in leaks.
Additionally, hydraulic fluid also heats up when compressed. If you don’t
select the proper temperature-rated hydraulic hose, then the inner tube may crack and deform, leading to fluid leaks and hydraulic hose failure at the fittings.
Abrasion
Hydraulic hoses are flexible, and when hydraulic fluid moves through them at high pressures, they experience jittering, expansion, and contraction. This movement causes internal stress that gets absorbed by the inner wire mesh linings of the hose. Depending on how the hose is routed, this movement may cause the hose to rub against external parts, leading to abrasion.
Over time, the wear and tear can become so severe that the metal braided or spiral core may become exposed, damaging the hose’s structural integrity to the point where it can no longer hold the fluid pressure. Proper maintenance and inspection maintenance programs can highlight worn-out hoses and prevent leaks and hydraulic hose failure so that your system runs smoothly.
Improper Bend and Erosion
Hydraulic hoses are fixed to other hydraulic components like pumps, valves, and cylinders via fittings. One end of the fitting is crimped onto the hose for a proper seal; however, if an improper fitting is used without the appropriate bend angle, it may cause the hose to tear against the sharp edges of the crimp seal –this one of the most common culprits of a hydraulic hose failure. As a result, the seal weakens, and intense fluid pressure may cause the hose to fly off from the fitting, spilling hydraulic fluid everywhere.
Erosion of the inner lining is another effect of having an incorrect bend at the fitting. This happens when hydraulic fluid forces out at high pressure and velocity and hits the hose’s inner liner if it’s overly crimped at the fitting. The fluid chips away at the inner polymer material, gradually thinning the lining. Over time, the lining may completely wear out and leak if not dealt with proactively.
Therefore, it is critical to comply with minimum
bend radius guidelines as stipulated by hose manufacturers.
How to Prevent Hydraulic Hose Failure
When hydraulic hoses fail, it is usually due to neglect. Make a checklist of all the hydraulic components before operating the machine and check for signs of damage on all hydraulic hoses after a set period. If any hose shows signs of damage, then replace it promptly to prevent any safety issues that may become hazardous to equipment and operators.