Brass or Stainless Steel in High-Pressure Hydraulics
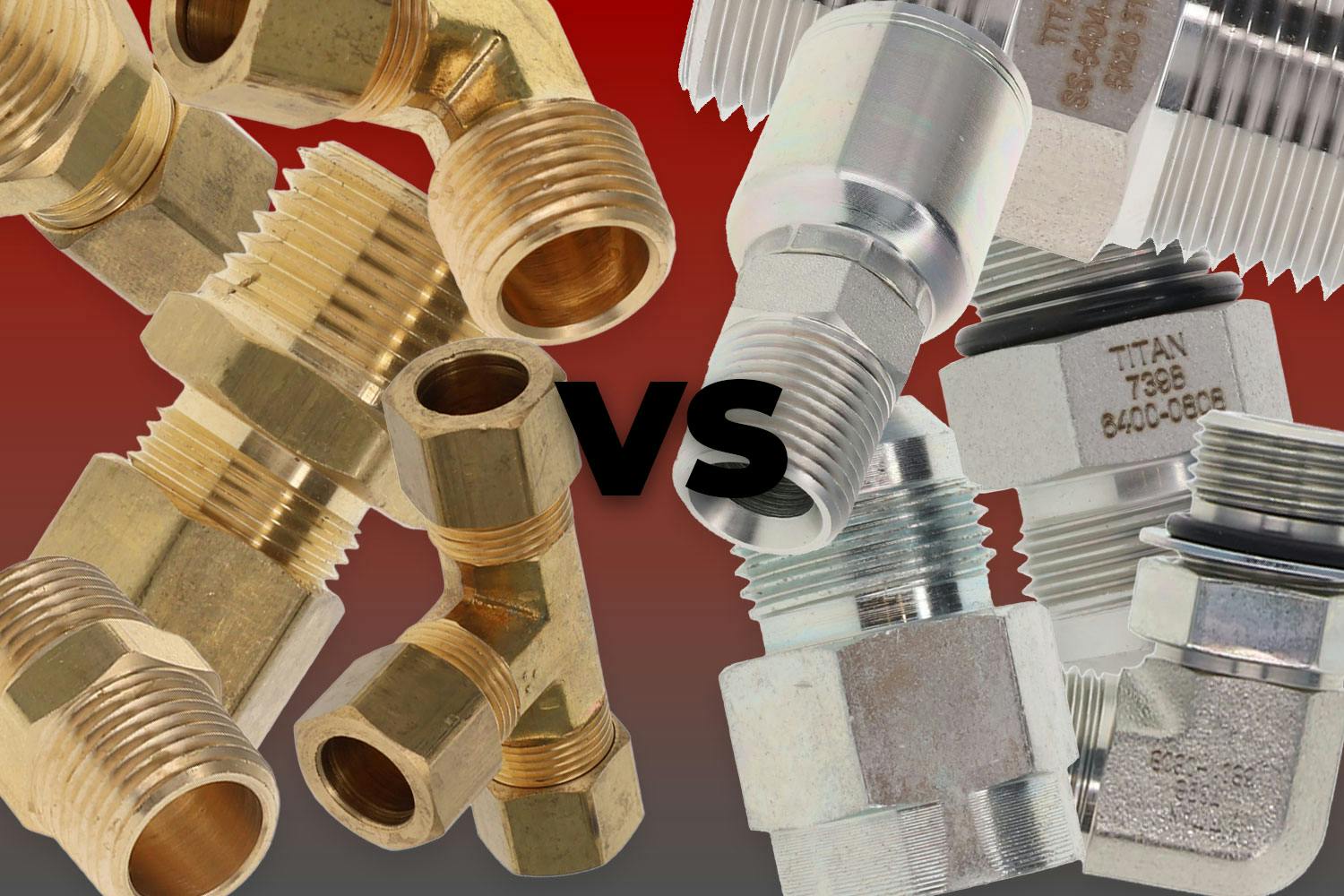
An Introduction to Selecting Brass or Stainless Steel in High-Pressure Hydraulics
In the intricate world of hydraulic systems, the choice of material plays a pivotal role, particularly in high-pressure systems. Two contenders often dominate the material debate: brass and stainless steel. Each possesses unique characteristics making them suitable for specific applications, but how do they fare under the rigorous demands of high-pressure hydraulics? This exploration aims to dissect the strengths and limitations of both materials in such demanding conditions.
The Critical Role of Materials in Hydraulics
Material selection in hydraulic systems isn't just about compatibility with fluids or cost-effectiveness; it's about survival under pressure — literally. In high-pressure environments, the material must withstand not just the operational pressures but also resist wear and corrosion over time. This resilience becomes a cornerstone for ensuring safety, efficiency, and longevity in hydraulic systems.
Brass in High-Pressure Applications: Pros and Limitations
Traditionally celebrated for its corrosion resistance and ease of machinability, brass is a common choice in moderate-pressure hydraulics. However, its behavior under high pressure is less straightforward. Brass, an alloy primarily of copper and zinc, offers reasonable strength but typically falls short in comparison to stainless steel when it comes to handling very high pressures. Its lower tensile strength makes it prone to deformation and failure under extreme stress, posing limitations in high-pressure applications.
- Brass fittings and components are commonly used in low to moderate pressure hydraulic systems.
- Typical PSI ratings for standard brass components range from 1,000 to 3,000 PSI.
- Certain brass alloys and specially designed components might handle pressures slightly higher than this range, but brass generally isn't used in the highest pressure applications.
Stainless Steel: The Preferred Choice for High-Pressure?
Enter stainless steel, a stalwart in the realm of strength and resilience. Known for its robust composition and superior corrosion resistance, stainless steel stands as the material of choice in many high-pressure environments. Its high tensile strength and ability to endure extreme conditions without yielding make it an ideal candidate for demanding hydraulic applications. Whether in marine environments or high-temperature settings, stainless steel consistently demonstrates an ability to withstand challenging conditions without compromise.
- Stainless steel is known for its strength and is used in medium to high-pressure hydraulic systems.
- Standard stainless steel hydraulic components can typically handle PSI ratings from 5,000 to 6,000, and often much higher.
- High-grade stainless steel and specifically designed components can withstand pressures upwards of 10,000 PSI or more.
Comparative Analysis: Brass vs. Stainless Steel under Pressure
When directly comparing these two materials under high-pressure scenarios, several factors come into play:
- Tensile Strength: Stainless steel typically outperforms brass, making it more suitable for applications involving high pressure.
- Corrosion Resistance: Both materials offer good corrosion resistance, but stainless steel edges out with its ability to resist a wider range of corrosive substances.
- Longevity: Under high-pressure conditions, stainless steel's robustness translates to a longer lifespan and less frequent need for replacement.
Real-World Applications and Case Studies
From the depths of oceanic exploration equipment to the high-pressure cylinders in industrial machinery, stainless steel's presence is ubiquitous. Conversely, brass finds its niche in less demanding applications where moderate pressures do not threaten its structural integrity. Examining case studies from industries like aerospace, maritime, and manufacturing provides tangible insights into how these materials perform in real-life high-pressure situations.
The Cost-Benefit Equation
Choosing between brass and stainless steel isn't merely a technical decision but also a financial one. Brass often appeals to budget-conscious projects due to its lower initial cost. However, for high-pressure systems where failure can result in significant costs or safety risks, the investment in stainless steel can be justified by its durability and reduced maintenance needs over time.
Conclusion: Making the Right Choice
Selecting the appropriate material for high-pressure hydraulic systems necessitates a balance of technical requirements, cost considerations, and application-specific demands. While stainless steel stands as a robust, reliable choice for high-pressure environments, brass may still find its place in applications where pressures are moderate, and cost constraints are tighter.
Ensuring Optimal Performance
To ensure optimal performance, regardless of the chosen material, regular maintenance, adherence to operational guidelines, and consideration of environmental factors are essential. Understanding the unique demands of your hydraulic system will guide you in making the most informed and effective material choice.
Frequently Asked Questions
How does the cost of brass compare to stainless steel in hydraulic systems?
Answer: Brass components are typically less costly upfront than their stainless steel counterparts. However, considering longevity and maintenance costs, stainless steel might be more cost-effective in the long run.
Is brass or stainless steel better for high-temperature applications in hydraulic systems?
Answer: Stainless steel is better suited for high-temperature applications. It maintains its strength and integrity at higher temperatures compared to brass.