Exploring Hydraulic and Fluid Systems in Semiconductor Manufacturing
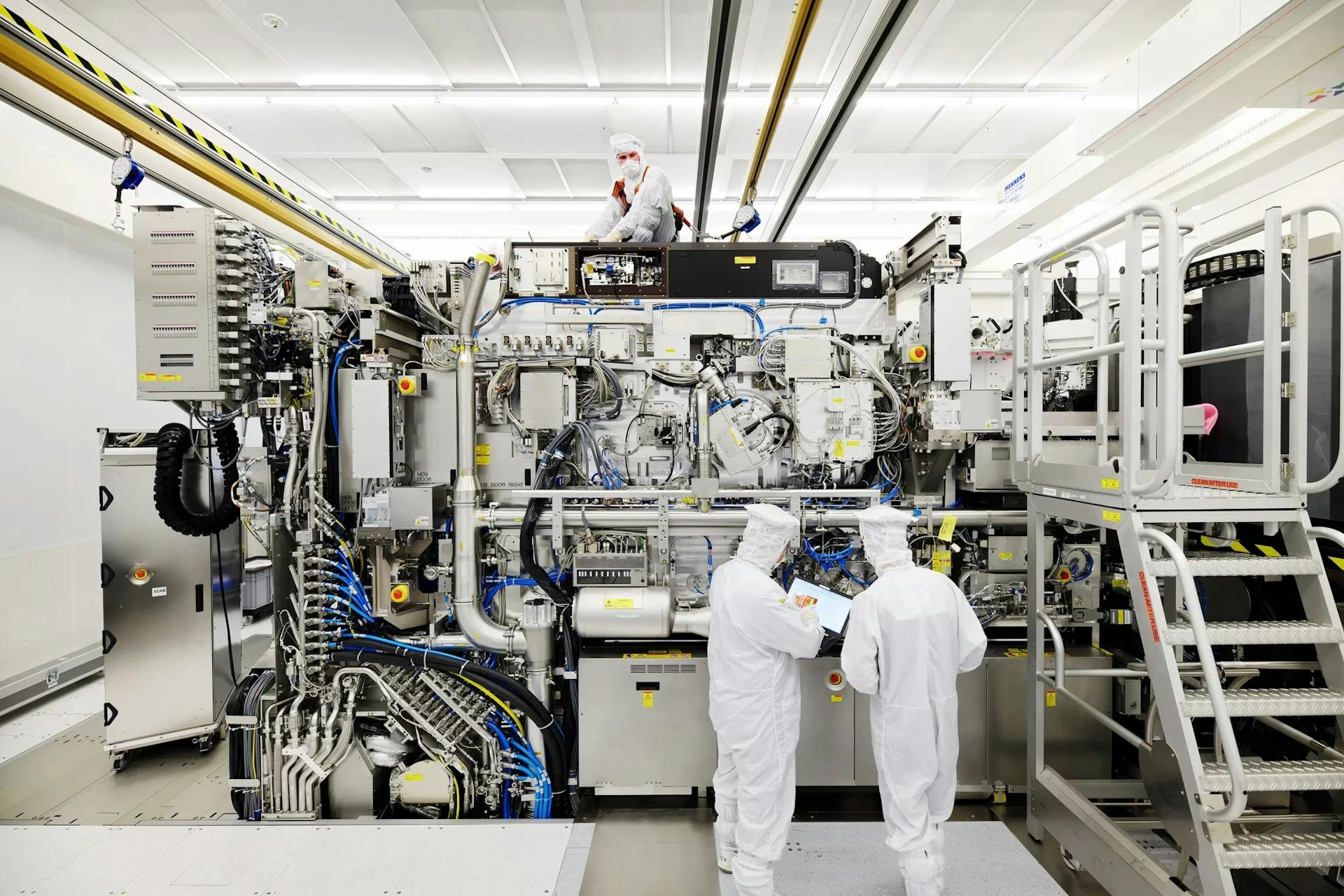
The Hydraulic Heartbeat of High-Tech
In the world of electronics, semiconductor manufacturing stands as a cornerstone of technological advancement, driving innovation across multiple industries. At the heart of this intricate manufacturing process lie the sophisticated hydraulic and fluid systems, which ensure the precision and cleanliness required for producing semiconductor devices. This blog explores the critical role of these systems, detailing how components such as metering pumps, diaphragm pumps, and precision dispensers are integral in processes ranging from chemical delivery to wafer cleaning and cooling systems. Understanding these components not only highlights the complexities of semiconductor fabrication but also underscores the importance of precise engineering in maintaining the industry's high standards.
1. Chemical Delivery
In semiconductor manufacturing, the delivery of chemicals is achieved through the use of sophisticated hydraulic and pneumatic systems. These systems are designed to handle a variety of substances, from volatile organic compounds to highly corrosive acids. For instance, during the etching process, strict amounts of an etchant must be applied to remove specific layers from the silicon wafer without damaging underlying structures. Flow control valves, pressure sensors, and automated feedback loops ensure that these substances are delivered at the correct rate and pressure, minimizing human error and maximizing process repeatability.
- Metering Pumps: These are used to deliver precise volumes of chemicals. Metering pumps can be adjusted for flow rate and pressure, ensuring accurate dispensing that meets the exact requirements of processes like etching and doping.
- Control Valves: Used to regulate the flow and pressure of chemicals. These valves are typically automated and can be finely tuned to ensure delivery.
- Flow Meters: Integral for monitoring the flow of chemicals. They provide real-time data to ensure that the specified amount of chemical is being used, helping to maintain process consistency and quality.
2. Wafer Cleaning
A "wafer" refers to a thin slice of semiconductor material, such as silicon, used as the substrate for fabricating integrated circuits (ICs) and other microdevices. Wafer cleaning requires meticulous handling to avoid any damage to the wafer's delicate surface. Fluid systems used in this process often include spray nozzles and rotary brushes that work in conjunction with high-purity deionized water and specialized cleaning chemicals. The cleaning solutions are delivered under controlled pressures to effectively remove contaminants while preserving the integrity of the wafer. Ultrasonic cleaning tanks may also be employed, where high-frequency sound waves create cavitation bubbles in the fluid, providing a gentle yet thorough cleaning action on the wafer surfaces.
- Diaphragm Pumps: These pumps are used to circulate cleaning solutions and water. They are chosen for their ability to handle corrosive fluids without leakage, which is critical for maintaining the purity of the cleaning agents.
- Spray Nozzles: These are designed to deliver cleaning fluids in a specific pattern and pressure, ensuring effective coverage and cleaning of the wafer surfaces.
- Ultrasonic Generators and Transducers: These components are used in ultrasonic cleaning systems to generate high-frequency sound waves that help remove contaminants from the wafer surface.
3. Efficient Cooling Systems
Cooling systems in semiconductor manufacturing must be capable of maintaining exact temperature control to prevent thermal damage to the silicon wafers and to ensure that the photolithographic patterns are accurately applied. These cooling systems typically use a combination of refrigerants and water-glycol mixtures to achieve the desired cooling effect. The flow of coolant is regulated by hydraulic pumps and valves, which adjust in real-time to changes in heat load to keep the temperature within strict tolerances.
- Centrifugal Pumps: These pumps circulate coolant throughout the system. They are capable of handling large volumes of fluid and can be adjusted to accommodate fluctuations in cooling demand.
- Heat Exchangers: Used to transfer heat from the coolant to a secondary fluid (often water or air), which is then cooled by other means. Heat exchangers must be highly efficient to maintain the calculated temperature conditions required.
- Thermostatic Valves: These automatically adjust the flow of coolant based on temperature feedback, ensuring that the equipment does not overheat.
4. Fluid Handling in Photolithography
The application of photoresist—a light-sensitive polymer—is a critical step in photolithography. This process requires extremely uniform thin film coating techniques. Spin coating is one popular method, where the wafer is spun at high speed while photoresist is dispensed onto its center. The centrifugal force spreads the photoresist evenly across the wafer's surface. The precision with which the fluid is dispensed, controlled by automated dosing systems, is crucial for achieving uniform thickness and consistent properties across the wafer.
- Precision Dispensers: These are used to apply photoresist and other coatings to the wafer. Dispensers must be capable of extremely accurate flow rates and droplet sizes to ensure uniform coverage.
- Spin Coaters: A device used to spin the wafer during application of photoresist. It includes a motor and speed control systems to ensure even distribution across the wafer.
- Solenoid Valves: These rapidly open and close to start and stop the flow of liquids, essential for the precise timing required in photolithography processes.
5. High-Purity Piping Systems
In the delivery of high-purity gases and liquids, the material selection for piping and fixtures (like valves and seals) is crucial to avoid contamination. Materials such as stainless steel, Teflon, and Vespel are commonly used because they do not react with the chemicals being transported. Moreover, the piping systems are designed with minimal bends and junctions to reduce places where particles can accumulate, and they are often installed with positive pressure or specialized filtration systems to prevent ingress of contaminants
- PFA (Perfluoroalkoxy) Tubing: This tubing is used for its non-reactive properties and smooth internal surface, which reduces the risk of contamination.
- Pneumatic Actuators: Often used to operate valves in the piping system, these actuators provide quick and reliable response to control signals.
- Filtration Units: These are integrated into the piping systems to remove particulates from fluids and gases before they reach critical areas.
Conclusion
The reliability of hydraulic and fluid system components are foundational to the sophisticated processes of semiconductor manufacturing. From metering pumps and control valves in chemical delivery to diaphragm pumps and spray nozzles in wafer cleaning, each component plays a critical role in ensuring the efficiency and cleanliness required at every stage. Moreover, the advanced technology behind these components, such as dispensers for photolithography and robust scrubbers for exhaust management, highlights the intricate balance of engineering excellence required in semiconductor production. Understanding and optimizing these hydraulic and fluid systems are crucial for maintaining high standards in semiconductor quality and yield, underpinning the technological advancements that drive our modern digital world.