Exploring the Intricacies of 300 Series Austenitic Stainless Steel
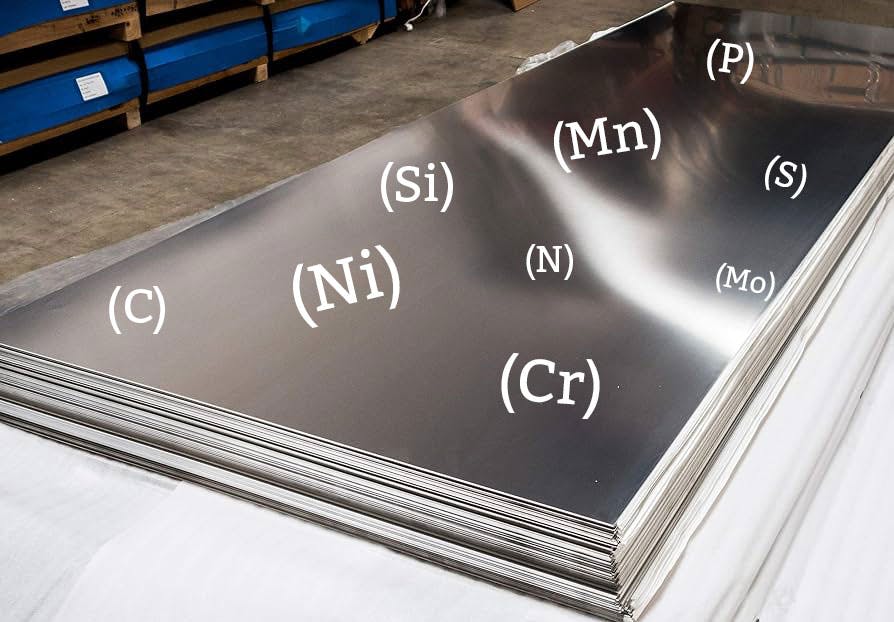
Introduction to 300 Series Austenitic Stainless Steel
In the realm of metallurgy, stainless steel stands as a marvel of modern engineering, epitomized by the 300 series austenitic grades. These stainless steels are known for their unique blend of strength, ductility, and resistance to corrosion. The 300 series, particularly grades 304 and 316, represent the pinnacle of this category, widely recognized for their surgical-grade quality and versatile applications.
The Foundation of Stainless Steel: Chromium
At the heart of all stainless steels is chromium. Constituting at least 10% of the alloy's weight, chromium is the game-changer that endows stainless steel with its signature stainless and corrosion-resistant qualities. This transformative element reacts with oxygen to form a protective layer, shielding the steel from environmental factors that would otherwise lead to rust and degradation.
304 Stainless Steel: The Versatile Workhorse
304 stainless steel, the most common grade in the 300 series, is a testament to the alloy's adaptability and reliability. Comprising 18% chromium and 8% nickel (sometimes referred to as 18/8 stainless), this grade is revered for its excellent corrosion resistance and formidable mechanical properties. Its versatility makes it an ideal candidate for a plethora of applications, from kitchenware to architectural frameworks.
316 Stainless Steel: The Corrosion-Resistant Champion
316 stainless steel takes corrosion resistance to the next level by incorporating molybdenum into its composition. With 16% chromium, 10% nickel, and 2% molybdenum, this grade is specially designed to withstand more saline or chloride-exposed environments. It is particularly favored in marine, chemical, and pharmaceutical applications where enhanced corrosion resistance is paramount.
A Comparative Look: 304 vs 316 Stainless Steel
While both 304 and 316 stainless steels are stars in their own right, they each shine brightest in different settings. 304's versatility makes it a first choice in environments where standard corrosion resistance suffices. However, in scenarios involving acidic or chloride-rich conditions, 316's molybdenum-enhanced composition makes it the superior choice for safeguarding against pitting and crevice corrosion.
Welding and Forming: The Common Strengths
Both 304 and 316 grades excel in welding and forming capabilities, a characteristic trait of the 300 series. This malleability allows for their use in complex shapes and structures, making them a favored choice across various industries. Notably, these alloys cannot be hardened through heat treatment but can develop high strength through cold working. For applications requiring both welding and forging, austenitic stainless steels like 304L and 316L are often the best choice due to their low carbon content (denoted by the letter L). They provide a good balance of weldability, corrosion resistance, and formability, which is beneficial in many industrial and construction applications.
Typical Uses Across Diverse Industries
The applications of 304 and 316 stainless steels span a wide array of industries. Grade 304 stainless steel, composed of 18% chromium and 8% nickel, is most widely used in kitchen appliances, sinks, and architectural paneling due to its excellent corrosion resistance and formability. It's an ideal choice for environments with exposure to a wide range of organic and inorganic materials but less so in saline or chloride-exposed conditions.
On the other hand, Grade 316 stainless steel, containing an additional element, molybdenum (typically 2-3%), significantly enhances corrosion resistance, especially against chlorides and marine environments. This makes 316 the go-to material for marine applications, chemical processing equipment, pharmaceutical production, and medical implants. While 316 is more expensive, its superior corrosion resistance in harsher environments justifies the cost for specific applications.
Super Austenitic Grades: Extending Performance
Beyond the conventional 304 and 316 grades, the super austenitic variants in the 300 series push the envelope in terms of performance. These high-nickel grades offer even greater corrosion and oxidation resistance, catering to extreme environments and applications requiring enhanced strength and resilience.
Compositions of Austenitic Stainless Steel
Frequently Asked Questions
1. What makes 304 and 316 stainless steel resistant to corrosion?
The key to their resistance lies in their chromium content, which forms a protective layer against corrosion. Additionally, the molybdenum in 316 stainless steel further enhances its resistance, especially in chloride-rich environments.
2. How does the addition of molybdenum enhance the properties of 316 stainless steel?
Molybdenum in 316 stainless steel significantly boosts its resistance to pitting and crevice corrosion, particularly in saline or chloride-exposed environments, making it a robust material for harsh conditions.
3. What are super austenitic grades, and how do they differ from 304 and 316?
These are high-nickel grades in the 300 series that offer superior corrosion and oxidation resistance. They are designed for extreme environments and applications requiring higher strength and resilience compared to standard 304 and 316 grades.
Shop Stainless Steel Instrumentation Fittings
Shop Stainless Steel Cast 150# Fittings
Shop Stainless Steel Forged 3000# Fittings