Forged vs Cast Stainless Steel: Understanding the Differences and Applications
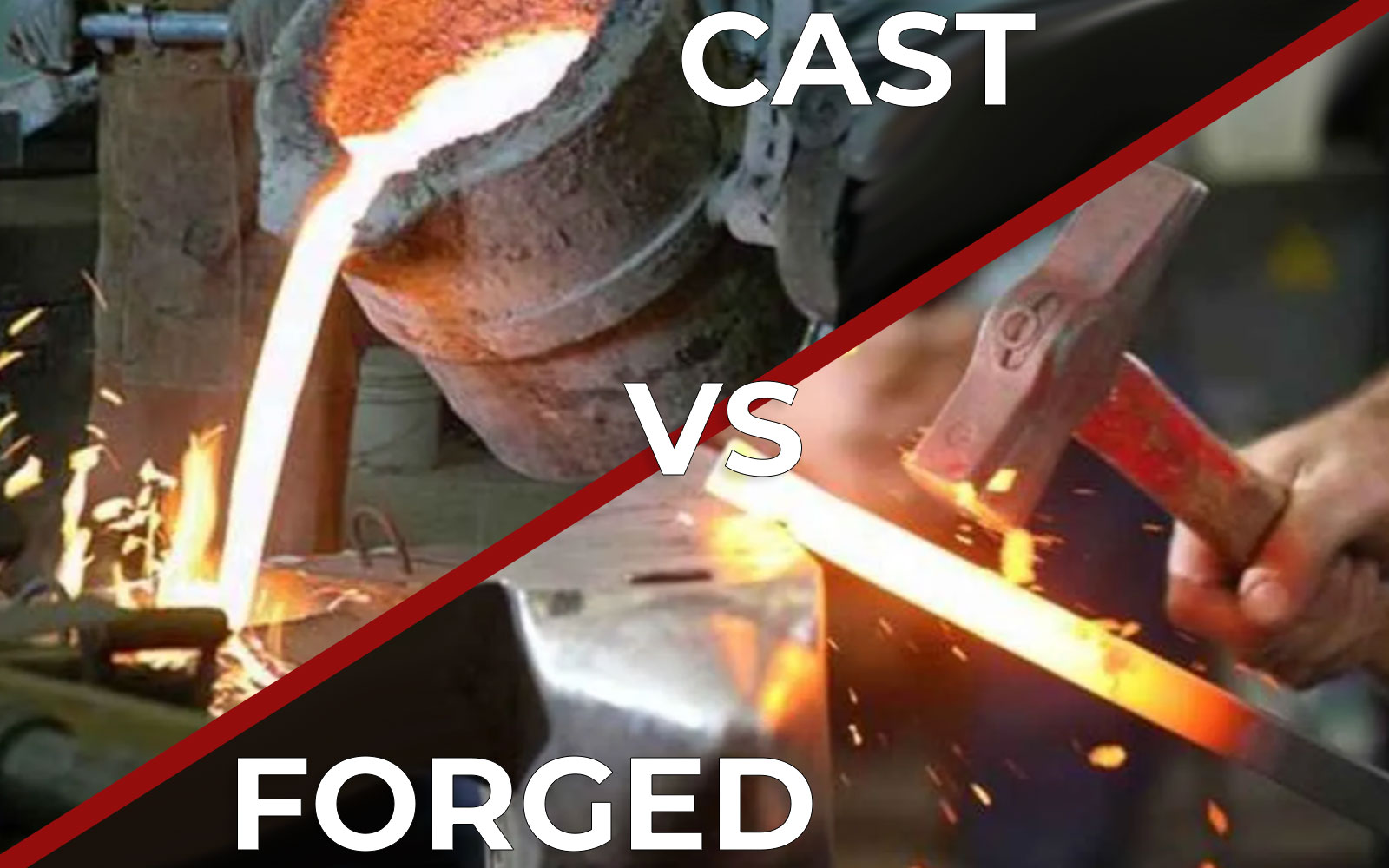
Forged vs Cast Stainless Steel: A Detailed Guide
When it comes to stainless steel, the debate between forged and cast forms is a hot topic. This guide breaks down the differences between forged and cast stainless steel, highlighting how these variations impact their performance and suitability for different applications.
What's the Difference?
In the professional sphere of metallurgy and engineering, the choice between forged and cast stainless steel hinges on their distinct scientific properties and industry applications. Forging, a process involving the deformation of heated steel through compressive forces, enhances the steel's strength and ductility. This method refines the grain structure, aligning it with the component’s shape, thereby enhancing tensile strength and toughness. Forged stainless steel, free from internal defects like porosity, is a staple in high-stress fields such as aerospace and automotive industries, where reliability and strength-to-weight ratios are crucial.
On the other hand, casting, which entails pouring molten steel into molds, excels in design flexibility and alloy versatility. This process allows the creation of complex shapes and intricate designs, with microstructure variability influenced by the cooling rate of the steel. Cast stainless steel, adaptable to a wide range of alloy compositions, finds its niche in industries requiring precision and aesthetic appeal, such as medical devices and architecture.
Strength and Durability
When we chat about strength and endurance, forged stainless steel is your go-to. It's like the superhero of metals – strong, reliable, and less prone to fatigue and stress. Forged parts are robust and more consistent, making them ideal for high-pressure and high-temperature applications. Think aerospace, automotive, and heavy machinery – places where you absolutely can't afford a material meltdown.
Cast stainless steel, while not as strong as its forged counterpart, has its own specialties. It’s great for intricate designs and complex shapes that forged steel might struggle with. It's the perfect candidate for custom designs where precision and aesthetics are key. You'll find it strutting its stuff in art, decorative architecture, and specialized machinery components.
Corrosion Resistance
Now, let's talk about playing the long game. Stainless steel is famous for its resistance to rust and corrosion, but does the manufacturing process make a difference? You betcha! Forged stainless steel has a more uniform structure, which means it's more resistant to corrosion over time. It's like having a shield against the elements, making it a smart pick for outdoor applications or environments with extreme temperatures and corrosive materials.
Cast stainless steel also holds its own in the battle against rust, especially in alloys designed for corrosion resistance. It’s often chosen for valves, pumps, and other equipment that need to resist the relentless attack of corrosive substances.
Cost and Production Time
Forged stainless steel is generally more expensive due to its labor-intensive process. It’s like paying for a custom-tailored suit: it takes more time and skill, but the fit and durability are unbeatable. However, the trade-off is a stronger and more reliable product.
Cast stainless steel is usually more cost-effective and quicker to produce, especially for complex shapes and designs. It’s like off-the-rack clothing: faster and more affordable, with a decent range of options.
When to Use Which?
So, when should you choose one over the other? Go for forged stainless steel when strength, durability, and uniformity are top priorities. It’s your go-to for high-stress applications where failure isn't an option.
Choose cast stainless steel when you need complex shapes, custom designs, or a more budget-friendly option that still offers good quality and corrosion resistance.
Conclusion
In the showdown between forged and cast stainless steel, it’s not about finding the ultimate winner, but rather understanding which hero fits your story best. Each process has its unique strengths and ideal applications, and the right choice depends on your project's specific needs.
Frequently Asked Questions
How do I decide between forged and cast stainless steel for my project?
Answer: Consider the application’s requirements: For high strength and durability under stress, choose forged. For intricate designs and cost-effectiveness, go with cast. Consulting with a material specialist can also provide tailored advice for your project.
Are there any applications where cast stainless steel is preferable over forged?
Answer: Cast stainless steel is ideal for complex shapes and detailed designs where forging is impractical. It’s a go-to choice for custom parts, intricate components, and decorative pieces.
What’s the main advantage of forged stainless steel over cast stainless steel?
Answer: Forged stainless steel boasts superior strength and durability. Its grain structure, altered through the forging process, makes it ideal for applications requiring high strength and resistance to wear and fatigue.