How Thread Galling Happens and Why Stainless Fittings Are the Worst Offenders
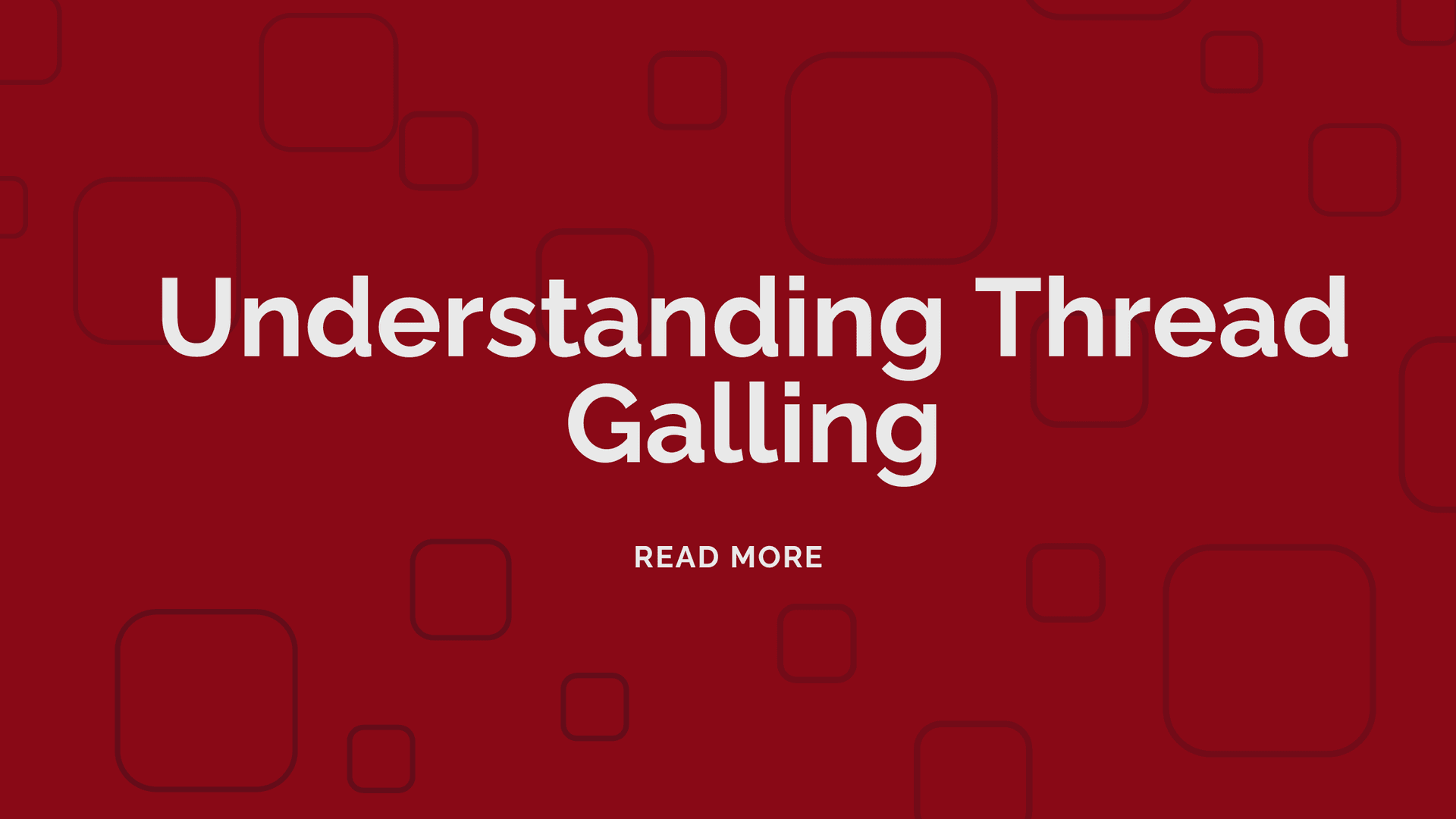
Thread galling is a significant issue in mechanical engineering and manufacturing, particularly when it comes to the use of stainless steel fittings. This phenomenon can lead to costly failures, increased maintenance, and even safety hazards. Understanding how thread galling occurs and why certain materials, especially stainless steel, are more susceptible to this issue is crucial for engineers, designers, and maintenance personnel alike.
Understanding Thread Galling
Thread galling is a type of wear that occurs when two metal surfaces come into contact and experience friction. This friction can lead to the transfer of material from one surface to another, causing the threads to seize or lock together. The result is often a damaged component that cannot be easily removed or reused.
The Mechanism of Galling
The process of galling begins when two surfaces made of similar materials are subjected to high pressure and friction. As the surfaces slide against each other, microscopic peaks and valleys on the metal surfaces can interlock. If the pressure is sufficient, these peaks can deform and tear away material from one surface, which then adheres to the other surface. This adhesion can create a bond that is stronger than the original material, leading to further damage and eventual failure.
Conditions That Favor Galling
Several factors can contribute to the likelihood of galling occurring. First, the type of material plays a crucial role. Softer metals are more prone to galling, especially when they are not lubricated. Additionally, the surface finish of the materials can influence the risk; rougher surfaces tend to gall more easily than smoother ones. Environmental conditions, such as temperature and humidity, can also impact the likelihood of galling, with higher temperatures often exacerbating the problem.
Why Stainless Steel Fittings Are the Worst Offenders
Stainless steel is often lauded for its durability and resistance to corrosion, making it a popular choice for fittings in various applications. However, these same properties can contribute to a higher incidence of thread galling, particularly in specific grades of stainless steel.
Material Properties of Stainless Steel
Stainless steel is an alloy that typically contains iron, chromium, and nickel. The addition of chromium provides corrosion resistance, while nickel enhances strength and ductility. However, the hardness of stainless steel can also lead to increased galling risk, especially when it comes into contact with other stainless steel components. When two stainless steel threads are tightened together, the friction can cause the material to adhere to itself, leading to galling. This phenomenon not only compromises the integrity of the fittings but can also result in costly downtime for repairs and replacements, making it a significant concern in industries that rely on reliable and durable connections.
Specific Grades and Their Susceptibility
Not all stainless steel grades are created equal when it comes to galling. For instance, austenitic stainless steels, such as 304 and 316, are particularly prone to galling due to their high ductility and work-hardening characteristics. In contrast, martensitic stainless steels, which are harder and more brittle, may experience less galling but can be more susceptible to other forms of wear and tear. Understanding the specific grade being used is essential for predicting galling behavior in threaded applications. Additionally, the environmental conditions in which these materials operate—such as temperature fluctuations, exposure to chemicals, and mechanical stress—can further influence their performance and susceptibility to galling, making it crucial for engineers and designers to consider these factors during the selection process.
Impact of Lubrication
One of the most effective ways to mitigate galling in stainless steel fittings is through the use of lubrication. Proper lubrication reduces friction between the threads, minimizing the risk of material transfer. However, not all lubricants are suitable for stainless steel applications. It is essential to choose a lubricant that is compatible with the specific environment and materials being used. Additionally, applying the right amount of lubricant can make a significant difference; too little may not provide adequate protection, while too much can lead to other issues, such as contamination. Furthermore, the choice of lubricant can also impact the overall performance of the fitting. For example, certain anti-seize compounds can provide additional protection against corrosion while also enhancing the ease of disassembly in the future. This is particularly important in applications where fittings may need to be serviced or replaced regularly, as it can save time and reduce the risk of damage during maintenance.
Preventative Measures for Thread Galling
While thread galling can be a serious issue, there are several strategies that can be employed to reduce the risk. By implementing preventative measures, engineers and maintenance personnel can help ensure the longevity and reliability of threaded connections.
Material Selection
Choosing the right material for threaded applications is crucial. In some cases, it may be beneficial to consider alternative materials that are less prone to galling. For instance, using a different grade of stainless steel or switching to a material such as brass or bronze can significantly reduce the risk. Additionally, the use of coatings or surface treatments can enhance the performance of stainless steel fittings and reduce galling potential.
Thread Design Considerations
The design of the threads themselves can also impact the likelihood of galling. Engineers should consider using threads with a larger pitch or a different profile to reduce the contact area between the two surfaces. Additionally, incorporating features such as relief grooves or undercuts can help minimize friction and allow for better lubrication distribution.
Proper Installation Techniques
Ensuring that threaded fittings are installed correctly is another critical factor in preventing galling. Over-tightening can lead to excessive pressure and friction, increasing the likelihood of galling. It is essential to follow manufacturer guidelines for torque specifications and to use appropriate tools for installation. Furthermore, regular maintenance and inspection of threaded connections can help identify potential issues before they escalate into more significant problems.
Conclusion: Addressing the Galling Challenge
Thread galling is a complex issue that can have significant implications for various industries. Understanding the mechanics behind galling and recognizing the specific challenges associated with stainless steel fittings is essential for mitigating risks. By selecting appropriate materials, employing effective lubrication strategies, and adhering to proper installation techniques, engineers and maintenance personnel can reduce the likelihood of galling and enhance the reliability of threaded connections.
As industries continue to evolve and push the boundaries of technology, the need for robust solutions to combat thread galling will remain a priority. Through ongoing research and development, as well as the sharing of best practices, it is possible to address this challenge and ensure the longevity and safety of critical components in mechanical systems.
Discover Reliable Solutions with Titan Fittings
Combat the challenges of thread galling with the superior quality of Titan Fittings. Our stainless steel fittings, hose fittings, valves, and adapters are engineered to withstand the high demands of hydraulic systems, ensuring maximum reliability and durability. For both standard and custom hydraulic fitting needs, Shop Now at Titan Fittings and secure the integrity of your industrial applications.