Optimizing Car Wash Performance with Advanced Hydraulic Equipment
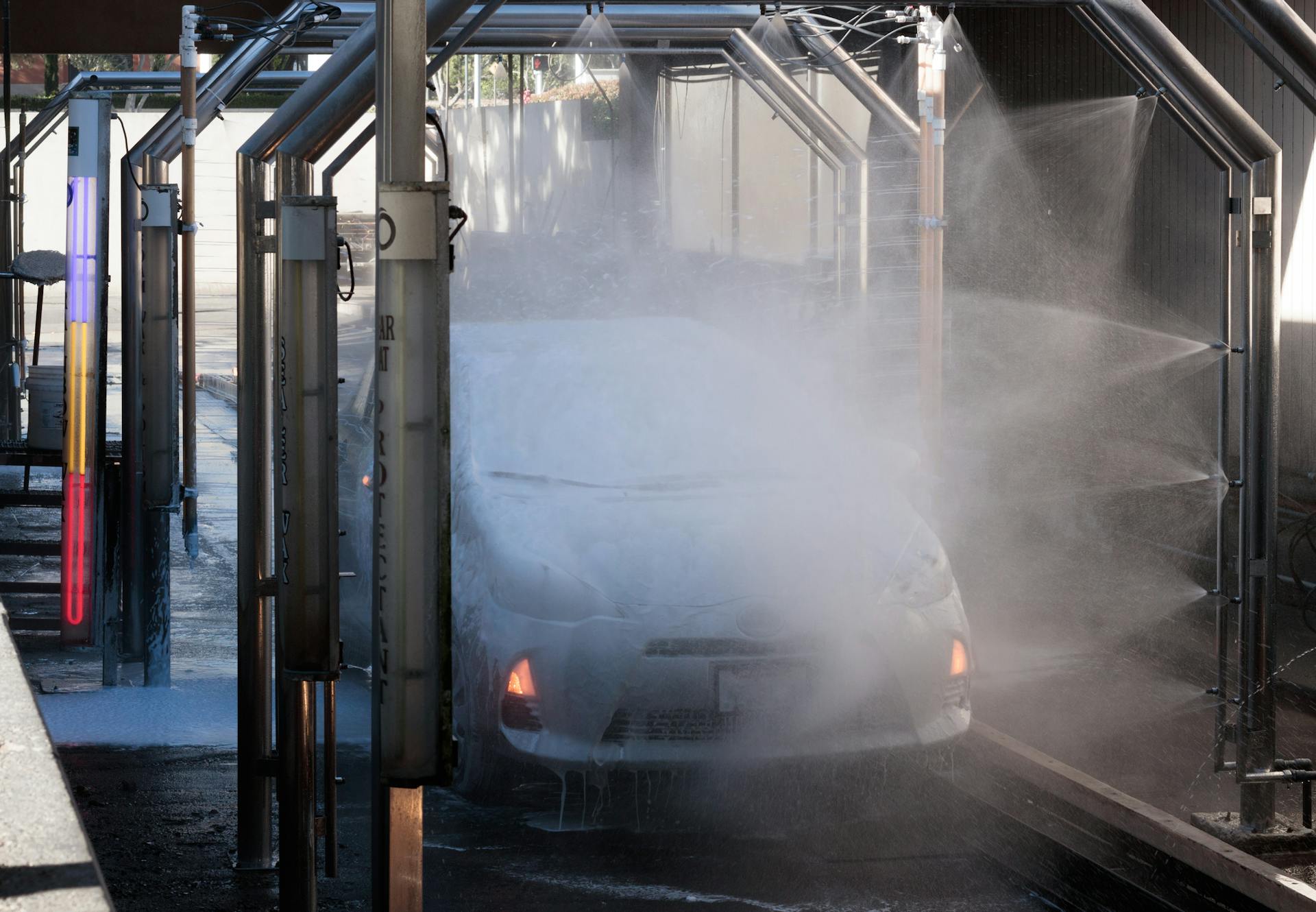
An Overview of Hydraulic Importance in Car Wash Efficiency
Automatic car washes are marvels of engineering efficiency, where every component plays a crucial role in delivering a quick, thorough clean. Central to these operations are hydraulic systems, which power everything from conveyors to high-pressure wash streams. This article examines the specific hydraulic equipment used in automatic car washes, focusing on both tunnel and in-bay configurations.
Benefits of Using Hydraulic Equipment in Car Washes
Hydraulic systems, especially when integrated with stainless steel components, are particularly beneficial in tunnel and in-bay automatic car washes, where durability, efficiency, and precision are paramount. In tunnel car washes, which handle a high volume of vehicles, the robustness of hydraulic systems ensures continuous operation without frequent maintenance interruptions. These systems provide the substantial force needed to move vehicles through the washing tunnel efficiently while managing various cleaning mechanisms that require precise control to adjust to different vehicle dimensions and shapes. This precise control is crucial to avoid damage to vehicles as they pass through different cleaning stages.
In the smaller, more compact setting of in-bay automatic car washes, the space-efficient design of hydraulic systems is a significant advantage. These systems maximize the use of limited space while delivering powerful cleaning actions necessary to thoroughly wash each vehicle. The quieter operation of hydraulic systems is also a benefit in in-bay settings, where noise reduction is important in typically more confined urban or residential locations. Moving forward we will break down the different hydraulic components used in automatic car wash systems.
Hydraulic Motors and Pumps in Car Wash Systems
Hydraulic motors and pumps are foundational components of automatic car wash systems, providing the essential power and control needed for efficient and effective operations. In these systems, hydraulic pumps convert mechanical energy into hydraulic energy, supplying the fluid power required to operate the motors that drive the various cleaning mechanisms, such as brushes, rollers, and conveyors.
- Hydraulic Pumps: In automatic car washes, pumps must deliver consistent hydraulic pressure and flow rate to ensure that the cleaning mechanisms operate smoothly and efficiently. These pumps are specifically designed to handle high-demand applications, ensuring that even during peak hours, the system's performance remains uninterrupted. The robust construction of these pumps minimizes wear and tear, reducing maintenance needs and extending the lifespan of the system.
- Hydraulic Motors: The motors in an automatic car wash system are tasked with translating hydraulic power into the mechanical motion needed to move brushes and rollers across the surfaces of vehicles. These motors are prized for their precise control capabilities, which allow for adjustments in speed and torque, adapting to the specific requirements of each washing cycle. This adaptability is crucial for achieving optimal cleaning without damaging the vehicle's exterior, especially when dealing with diverse vehicle sizes and shapes.
The integration of hydraulic motors and pumps in car wash systems also allows for a reduction in energy consumption compared to other mechanical systems. By precisely matching power output to the demand, hydraulic systems avoid the energy wastage common in less adaptable solutions. This efficiency not only conserves energy but also reduces operational costs over time.
Conveyor Systems: The Heartbeat of Tunnel Washes
Hydraulic conveyor systems play a pivotal role in the functionality of automatic car washes, facilitating the smooth and continuous movement of vehicles through the cleaning process. These systems are engineered to deliver the strength and precision required to handle vehicles of varying sizes and weights, ensuring they are safely and efficiently transported through different wash stages.
- Robust Operation: Hydraulic conveyors are chosen for their robustness, capable of operating under the high-load conditions typical in busy car wash environments. Unlike mechanical or pneumatic systems, which may struggle with the weight and constant movement of vehicles, hydraulic conveyors provide the necessary power to move vehicles steadily and reliably. This continuous operation is crucial for maintaining a high throughput, especially during peak business hours, ensuring that customer wait times are minimized.
- Precise Speed Control: One of the standout features of hydraulic conveyor systems is their ability to precisely control the speed of the conveyor belt. This is essential in automatic car wash systems where the timing of each wash phase must be meticulously managed to align with specific cleaning functions. Whether it's pausing for an extra scrub on heavily soiled areas or synchronizing with undercarriage washes, hydraulic conveyors can adjust their speed to optimize the cleaning results without compromising the safety of the vehicle.
High-Pressure Wash Streams Powered by Hydraulics
High-pressure wash systems are essential components of automatic car washes, providing the intense cleaning power needed to remove dirt, grime, and environmental pollutants from vehicles effectively. These systems leverage the robustness and precision control of hydraulic technology to deliver water and cleaning solutions at high pressures, ensuring a thorough clean without damaging the vehicle's surface.
- High-Pressure Cleaning Efficiency: Hydraulic high-pressure wash systems are capable of producing significantly greater water pressure than traditional electric or pneumatic systems. This high pressure is crucial for dislodging tough dirt and road residue that standard washing methods might miss. The force exerted by these systems can be finely adjusted to suit different types of vehicles and levels of soil, providing a customized wash that targets specific areas as needed.
- Energy and Water Efficiency: Hydraulic systems are known for their energy efficiency, as they only consume power when needed and can operate at peak efficiency under variable loads. This efficiency translates into lower operational costs and a smaller environmental footprint. Additionally, the precision control offered by hydraulic systems allows for optimal water usage, reducing waste and minimizing the overall consumption of water and cleaning agents.
- Enhanced Customer Satisfaction: The effectiveness of hydraulic high-pressure wash systems in removing even the most stubborn dirt enhances customer satisfaction by delivering a noticeably cleaner vehicle. The speed and efficiency of these systems also contribute to faster service times, reducing wait times for customers and increasing throughput for the business.
Hydraulic Cylinders and Actuators: Essential for Precision
Hydraulic cylinders and actuators play pivotal roles in the mechanics of automated car washes, ensuring that various components operate smoothly and effectively. These hydraulic devices are fundamental in driving the movement and control of the equipment necessary for a comprehensive and safe car wash experience.
- Movement and Control of Wash Equipment: Hydraulic cylinders and actuators are primarily responsible for the precise movement and positioning of brushes, rollers, and spray nozzles. They adjust dynamically to the size and shape of each vehicle, ensuring that all surfaces are reached and cleaned thoroughly without causing damage. This adaptability is crucial for maintaining high-quality cleaning standards across a wide range of vehicle types.
- Pressure Application for Cleaning Tools: In addition to moving equipment, hydraulic cylinders provide the necessary force to press washing tools against the vehicle. This pressure must be carefully controlled to be effective yet gentle enough to prevent damage to the vehicle’s paint and detailing. The robust nature of hydraulic systems allows for this force to be applied consistently and reliably.
- Operation of Gates and Conveyors: Hydraulic actuators are also used to operate gates and guide rails that help position and move vehicles through the car wash tunnel. Their smooth and controlled operation is essential for the seamless transition of vehicles from one cleaning station to the next, enhancing the efficiency of the washing process.
Precision Control with Hydraulic Valves and Controls
Hydraulic valves and controls are essential components in automated car wash systems, enabling precise management of the hydraulic circuits that drive the entire operation. These components regulate the flow, pressure, and direction of hydraulic fluid, ensuring that all hydraulic machinery functions harmoniously and efficiently. This section details the critical role and functionality of hydraulic valves and controls in automated car washes.
- Regulation of Hydraulic Flow and Pressure: Hydraulic valves are crucial for controlling the flow and pressure of the hydraulic fluid within the system. In an automated car wash, different stages of the wash cycle require varying levels of force and speed. For example, hydraulic valves adjust the pressure for brush movements to ensure they are forceful enough to clean effectively but gentle enough to avoid damaging the vehicle. By precisely controlling these parameters, hydraulic valves ensure optimal performance of cleaning mechanisms, such as brushes, rollers, and spray nozzles.
- Directional control valves play a pivotal role in guiding the hydraulic fluid's flow path throughout the car wash system. These valves can switch the direction of fluid flow, enabling machinery to move in different directions or transition between operational states. This capability is essential for activating different parts of the car wash, like lifting barriers or moving brushes, in a coordinated manner according to the washing cycle's requirements.
- Enhanced System Efficiency and Response: Hydraulic controls, including servos and sensors integrated with the valves, enhance the responsiveness and efficiency of the system. These controls allow for real-time adjustments based on various operational conditions, such as changes in vehicle size or processing speed. For instance, sensors can detect a vehicle’s presence and dimensions, prompting the hydraulic system to adjust the water pressure or the positioning of the brushes accordingly.
- Safety Features:Safety is a paramount concern in automated systems, and hydraulic valves incorporate several safety features to prevent failures and accidents. Pressure relief valves are designed to open at a preset limit to avoid excessive pressure buildup that could lead to hydraulic system failure or damage to the car wash equipment or vehicles.
Benefits of Using Stainless Steel in Car Washes
A key advantage of incorporating stainless steel into hydraulic components is its excellent corrosion resistance, crucial in the wet and chemically active environment of a car wash. Stainless steel prevents bacterial growth, maintaining hygiene while also enhancing the aesthetic appeal of the equipment with its sleek, modern look. Despite a higher initial cost, the longevity and minimal maintenance of stainless steel parts provide a cost-effective solution over time, making them an economically advantageous choice for car wash businesses aiming to deliver high-quality service with minimal operational interruption.
Conclusion
Hydraulic equipment is indispensable in the operation of both tunnel and in-bay automatic car washes. From driving conveyor belts to powering high-pressure wash systems, hydraulics provide the strength, durability, and precision necessary for modern car washes to operate efficiently and effectively.
Upgrade your car wash system with superior hydraulic technology. Contact us today to discover how our hydraulic solutions can optimize your operations, ensuring peak performance and customer satisfaction.