Passivation of Stainless Steel Parts
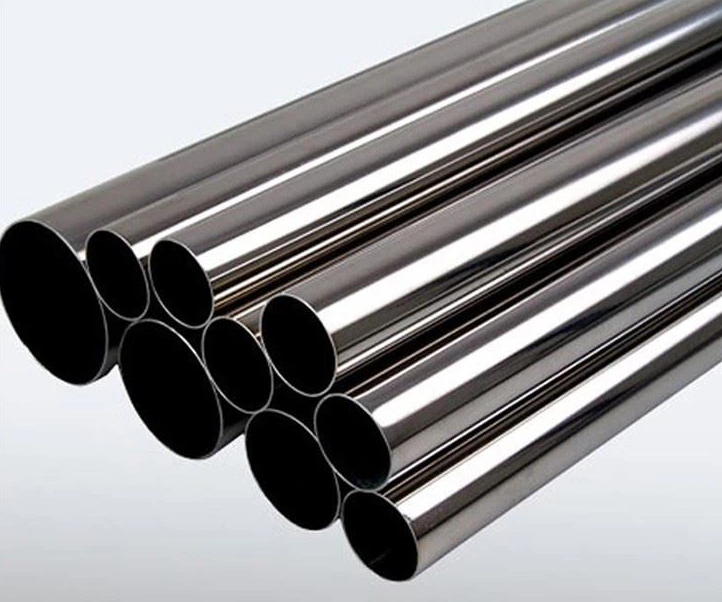
Passivation of Stainless Steel Parts
Passivation of stainless steel parts is a crucial process in various industries, such as aerospace, defense, electronics, and medical. It involves the formation of a passive layer on the surface of stainless steel to enhance its corrosion resistance and extend its lifespan. By understanding the science behind passivation, exploring the various types and techniques, and examining its applications, we can gain a deeper appreciation for the importance of passivation for the protection of stainless steel parts. In this blog, we will delve into the key terms, chemical processes, and benefits of passivation, as well as discuss its challenges and safety measures.
Understanding Passivation
Passivation is a process that aims to enhance the corrosion resistance of stainless steel parts by removing free iron particles and forming a passive layer on their surface. These free iron particles can react with environmental factors, leading to corrosion, oxidation and discoloration of the metal. Passivation eliminates these free iron particles and forms a protective oxide layer, commonly referred to as a passive layer.
Key Terms in Passivation
Free iron, if left unaddressed, can act as a catalyst for corrosion. The objective is to remove it from the surface of stainless steel parts. By eliminating free iron, passivation creates a clean surface, free from contamination, and promotes the formation of a passive film.
The passive film, also known as a protective oxide layer, is a critical component of passivation. It is a thin layer of metal oxide that forms on the surface of stainless steel parts during the passivation process.
Surface contamination, such as dirt, oil, grease, and other foreign matter, can interfere with the passivation process. Prior to passivation, thorough cleaning and preparation of the stainless steel surface are essential to remove surface contaminants and ensure the effectiveness of the passivation treatment.
Conversion coating is another term associated with passivation. It refers to the chemical treatment of stainless steel parts to enhance their corrosion resistance and improve their surface finish. The passivation process is one type of conversion coating, focusing specifically on stainless steel parts to promote the formation of a protective oxide layer.
The Science Behind Passivation
The science behind passivation lies in the chemical reactions that occur during the process. When stainless steel parts are immersed in a passivating solution, a series of reactions take place on the surface.
Treatments such as citric acid or nitric acid passivation initiate chemical reactions with the stainless steel surface, resulting in the formation of a passive layer. This passive layer, composed of metal oxide, acts as a protective barrier, preventing corrosion and improving the stainless steel's resistance to environmental factors.
Understanding the chemical processes involved in passivation and how they contribute to the formation of the passive layer is crucial in optimizing the treatments.
Types and Techniques of Passivation
There are various types and techniques of passivation that offer different advantages, depending on specific requirements and industry applications. Two commonly used passivation methods are citric acid passivation and nitric acid passivation. Each technique has its unique properties and benefits, making them suitable for different scenarios.
Citric Acid Passivation
Citric acid passivation, utilizing the natural acid from citrus fruits, has emerged as a popular method in industries like medical and food processing due to its environmental friendliness and lower toxicity compared to nitric acid passivation. This technique is not only safer to handle and dispose of, but it also meets stringent industry standards, providing reliable corrosion resistance and a clean finish free from impurities, crucial for applications demanding high cleanliness levels. Offering a viable alternative to nitric acid passivation, citric acid passivation effectively maintains surface quality while aligning with specific environmental concerns and safety requirements in sensitive sectors.
Nitric Acid Passivation
Nitric acid passivation stands out in the realm of metal finishing, particularly for stainless steel, due to its exceptional ability to bolster corrosion resistance, ensure surface cleanliness, and effectively remove residual acids. This process is governed by stringent industry standards, including surpassing salt spray test requirements, which measure the material's ability to withstand corrosive environments. During nitric acid passivation, stainless steel components are submerged in a nitric acid solution, a step crucial for the development of a dense, protective chromium oxide layer on the metal's surface. This passive layer is instrumental in shielding the steel from various forms of corrosion, thereby significantly enhancing its longevity and durability.
Nitric acid passivation stronger oxidizing properties and faster reaction time enable it to more aggressively remove iron and other contaminants from stainless steel surfaces. This results in a quicker and more robust formation of the passive chromium oxide layer, offering enhanced corrosion resistance, particularly for high-carbon steel grades or in highly corrosive environments. While nitric acid allows for greater operational flexibility in terms of temperature and concentration, it also poses more significant safety and environmental challenges compared to the milder, eco-friendlier citric acid passivation, making nitric acid passivation a choice for applications where maximum corrosion resistance is imperative, albeit with added handling and disposal considerations.
Role of Oxidation in the Passivation Layer
Oxidation plays a vital role in the formation of the passivation layer on stainless steel parts. It involves the interaction of chromium, oxygen, and other elements present in the stainless steel alloy.
Chromium, an essential component of stainless steel, reacts with oxygen in the passivating solution, forming a chromium oxide layer on the surface of the stainless steel parts. This process, known as oxidation, enhances the corrosion resistance of the stainless steel by creating the passive layer.
The chromium oxide layer acts as a shield, preventing direct contact between the metal surface and corrosive agents. It reduces the potential for metal degradation, such as flash attack, oxide scale formation, corrosion and discoloration by providing a protective barrier against chemical reactions that could lead to surface deterioration.
The Procedure of Passivating Stainless Steel
The procedure involves preparation and cleaning of the stainless steel surface to remove contaminants. Next, applying passivation chemicals like citric acid baths or nitric acid baths promotes the formation of a chromium oxide layer for surface passivation. Finally, rinsing and drying the parts are crucial for the successful completion of the passivation process to enhance corrosion resistance and durability. Regular intervals of passivation are necessary to maintain the quality of metal surfaces in manufacturing processes, ensuring the effectiveness of the passivation layer.
1) Preparation and Cleaning
Key steps before passivating stainless steel parts include thorough cleansing to eliminate contaminants. Preparation necessitates degreasing and cleaning for effective passivation. Cleaning also aids in achieving the desired surface finish. Removal of surface impurities is a prerequisite before initiating the treatment. The process involves ensuring that the parts are free from any unwanted substances like iron particles or oils/grease.
2) Applying Passivation Chemical
Enhancing stainless steel surfaces involves the immersion of parts in a solution to form a protective layer. The immersion time for stainless steel parts in a passivation solution can vary depending on several factors including the type of stainless steel, the passivation method used (citric acid or nitric acid), and the specific requirements of the part. It's essential to refer to the ASTM standards (like ASTM A967 for citric acid passivation and ASTM A380 for nitric acid passivation) for more detailed guidelines and to ensure that the process meets the required specifications.
3) Rinsing and Drying
Ensuring thorough rinsing of stainless steel parts post-passivation eliminates lingering chemicals, vital for surface purity. Subsequent drying is pivotal to prevent water spot formation and corrosion, preserving metal integrity during the process. Adherence to meticulous rinsing and drying protocols significantly enhances the efficacy of the passivation process by removing all remnants of chemicals, safeguarding metal durability. Complete removal of chemical substances through rinsing is imperative for sustained protection. Thorough drying maintains the integrity of the crucial oxide layer that is formed during passivation.
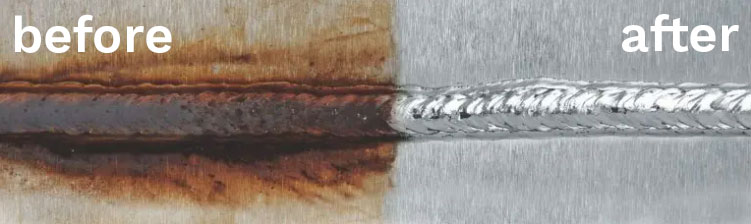
The Challenges of Passivation
Despite its benefits, challenges may arise, such as the need for regular intervals of sodium dichromate treatments to uphold the passivation layer’s integrity. Manufacturers must be aware of potential issues that can occur during passivation, necessitating a thorough understanding of conversion coatings applied in such cases.
Potential Issues and How to Avoid Them
During passivation, issues like corrosion or discoloration can occur, especially if not done correctly. Choosing the right passivation method based on the stainless steel type and part's purpose is vital. To avoid problems, thorough cleaning and proper handling before and after passivation are recommended. Partnering with experienced passivation providers ensures the effectiveness of the process, leading to optimal results.
Safety Measures During Passivation Process
Safety precautions are crucial during the passivation of stainless steel due to the utilization of different chemicals that can be potentially dangerous. Ensure proper personal protective equipment, like gloves and eye protection. Work in well-ventilated spaces to prevent inhalation of fumes. Adhere strictly to manufacturer guidelines for solution concentrations. Thoroughly rinse components post-passivation to eliminate any leftover chemicals. Dispose of solutions and rinse water according to local regulations to maintain safety standards.
Key Equipment in Stainless Steel Passivation
In the realm of stainless steel passivation, a range of specialized equipment is essential for ensuring both the efficiency and effectiveness of the process. Central to this are acid-resistant passivation tanks or baths equipped with temperature control systems for immersing parts in the solution. Following passivation, spray rinse stations and drying ovens ensure the complete removal of residual acids and moisture. Automated handling systems, including conveyors and robotic arms, facilitate smooth transitions between passivation, rinsing, and drying stages. Pre-passivation cleaning may involve ultrasonic cleaners for thorough decontamination. The process's integrity is monitored using tools like pH meters and solution analyzers, while the safety of operators is ensured through appropriate personal protective equipment (PPE).
H2: Frequently Asked Questions
What is passivation?
Passivation involves a chemical process that eliminates free iron from stainless steel surfaces, enhancing their corrosion resistance with a protective oxide layer. This technique prevents rust, staining, and corrosion, crucial for industries needing durable components.
Does stainless steel need passivation?
Stainless steel does benefit from passivation. This process helps to ensure the longevity and corrosion resistance of stainless steel components. It's recommended to passivate stainless steel after fabrication or machining to enhance its performance and durability.
What chemicals are used in passivation?
The chemicals commonly used in passivation include citric acid, nitric acid, and sodium dichromate. These chemicals help to clean the metal surface, remove impurities, and promote the formation of the protective oxide layer.
Can I passivate carbon steel?
The passivation of carbon steel involves applying external protective coatings or treatments to prevent corrosion, unlike the natural oxide layer formation in stainless steel. Techniques include oiling, painting, or other corrosion inhibitors, and sometimes controlled oxidation processes. These coatings act as a barrier against environmental elements but are more prone to damage and wear, requiring regular maintenance and reapplication, unlike the self-healing chromium oxide layer on stainless steel.
What Factors Influence the Success of the Passivation Process?
1) Chromium content vital for the oxide layer
2) Correct immersion duration
3) Consideration of surface grain boundaries
4) Maintaining ideal conditions like temperature and solution strength
5) Recognizing unique requirements for varied metals
Shop our Stainless Steel Compression Fittings