What is a Hydraulic Cylinder?
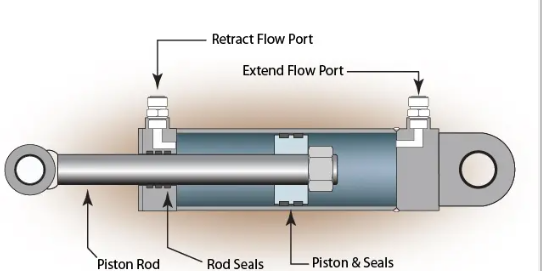
What is a Hydraulic Cylinder?
What is a hydraulic cylinder and how does it work?
A hydraulic cylinder is a mechanical device that uses hydraulic fluid to generate force in a linear motion. It consists of a cylinder barrel, piston, piston rod, and hydraulic fluid. When hydraulic pressure is applied, the piston moves, pushing or pulling the load with it.
Hydraulic cylinders are mechanical devices that play a crucial role in numerous industries, from manufacturing to construction and material handling. These powerful cylinders use hydraulic energy to generate linear force and motion, making them essential components in various applications. Understanding the basics of hydraulic cylinders, including their components, functionality, and key specifications, is essential for professionals working with hydraulic systems. In this blog, we will explore the definition, purpose, working principles, components, types, applications, and factors to consider when selecting hydraulic cylinders.
Understanding the Basics of Hydraulic Cylinders
When it comes to hydraulic power, understanding the basics of hydraulic cylinders is essential. These cylinders are mechanical devices that convert hydraulic energy into mechanical energy, performing linear work in the process. By exerting force through a piston, hydraulic cylinders enable mechanical movement and control in various industrial applications. Whether it's heavy machinery, construction equipment, or material handling systems, hydraulic cylinders play a critical role in transferring hydraulic pressure into mechanical force.
Definition and Purpose
At their core, hydraulic cylinders are devices that harness hydraulic energy to generate linear force and motion. By converting the pressure of hydraulic fluid into mechanical energy, these cylinders are able to perform a wide range of tasks in different industries. One of the primary purposes of hydraulic cylinders is to provide an efficient and reliable means of converting hydraulic energy into mechanical movement. This allows for precise control over the movement of machinery, equipment, and other mechanical systems. The construction of hydraulic cylinders is designed to ensure durability and reliability, meeting industry standards and withstanding the demands of various applications. From heavy-duty construction equipment to material handling systems, hydraulic cylinders are essential components in a wide range of industries.
How a Hydraulic Cylinder Works?
Understanding how a hydraulic cylinder works is fundamental to comprehending its importance in hydraulic systems. Hydraulic cylinders operate on the principle of converting hydraulic energy, provided by hydraulic fluid, into mechanical movement. The cylinder consists of a piston that moves back and forth within a cylinder bore, creating mechanical force. When hydraulic fluid is directed into the cylinder, it pushes the piston, causing it to extend or retract, depending on the hydraulic system's requirements. This mechanical movement is then transferred to the load or machinery, enabling precise control and efficient operation. The bore diameter, piston design, and hydraulic pressure all play crucial roles in determining the mechanical movement generated by hydraulic cylinders.
The Components of a Hydraulic Cylinder
To better understand hydraulic cylinders, it is important to familiarize oneself with their key components. Each component performs a specific function and contributes to the overall efficiency and reliability of the hydraulic cylinder. The main components include the cylinder barrel, piston, piston rod, cylinder base or cap, cylinder head, and seals. By examining each component in detail, we can gain a deeper understanding of how hydraulic cylinders operate and why they are vital in hydraulic systems.
Cylinder barrel
The cylinder barrel serves as the main body of the hydraulic cylinder, housing the piston and other internal components. It is typically made from durable materials, such as steel or other alloys, to withstand high pressure and mechanical forces. The bore of the cylinder barrel provides a smooth inner surface for the piston to move freely without excessive friction. Additionally, some cylinder barrels may have special coatings to enhance corrosion resistance and reduce wear. Proper selection and maintenance of the cylinder barrel are crucial for ensuring the long-term performance and reliability of hydraulic systems.
Piston
The piston is a vital component of hydraulic cylinders, responsible for generating the linear force required for mechanical movement. It moves back and forth within the cylinder barrel, exerting pressure on the hydraulic fluid to create movement. Pistons are typically made from durable materials, such as steel, and may undergo special treatments or coatings to enhance their corrosion resistance. The design of the piston, including its diameter and surface finish, plays a key role in determining its efficiency and longevity. Manufacturers like Enerpac offer a range of high-quality pistons that meet strict industry standards, ensuring reliable performance in hydraulic systems.
Piston rod
The piston rod extends from the piston and transmits the force generated to the external load or machinery being operated. Made from high-strength materials, such as chrome-plated steel, piston rods are designed to withstand high pressure and bending forces. The diameter and fittings of the piston rod are carefully selected to provide optimal strength and stability. Plating, such as chrome plating, enhances corrosion resistance and reduces wear and tear on the piston rod. Proper installation and maintenance of the piston rod are critical for ensuring safe and reliable operation of hydraulic cylinders.
Cylinder base or cap
The cylinder base, also known as the cap, serves as the mounting point for the hydraulic cylinder and facilitates force transmission. It is typically secured to the cylinder barrel, creating a sealed chamber for hydraulic fluid. The construction and design of cylinder bases may vary depending on the specific application requirements. Some cylinder bases may include accessories, such as fittings or valve arrangements, to enhance the functionality of hydraulic systems. In construction equipment, for example, cylinder bases may be equipped with specific accessories to optimize performance and safety.
Cylinder head
The cylinder head encloses the hydraulic cylinder, providing access for piston rod attachment and seal containment. It may also house bearings to support the piston rod's movement and ensure smooth operation. Cylinder heads are designed with precision machining to ensure proper alignment and seal integrity. In high-pressure hydraulic systems, cylinder heads are engineered to withstand the force exerted by hydraulic fluid, with their specifications, including pressure resistance measured in pounds per square inch (psi). Proper sealing and control mechanisms in cylinder heads are essential for hydraulic system safety and performance.
Seals
Seals are integral components of hydraulic cylinders, responsible for preventing fluid leakage, maintaining pressure, and protecting internal components from contamination. These seals are typically made from specialized materials, such as rubber or synthetic compounds, and are designed to withstand hydraulic fluid, temperature, and wear. Seal specifications may include factors such as National Pipe Thread (NPT) size, material compatibility, and resistance to corrosion. Proper selection, installation, and maintenance of seals are crucial for ensuring the long-term efficiency and reliability of hydraulic cylinders. The key considerations for seals in hydraulic cylinders include:
- Compatibility with hydraulic fluid
- Resistance to wear and temperature extremes
- Proper installation and alignment
- Regular inspection and replacement as needed
Types of Hydraulic Cylinders
Hydraulic cylinders come in various types, each designed to cater to specific application requirements. Understanding the different types of hydraulic cylinders is important when selecting the right one for a particular project or system. Common types include single-acting cylinders, double-acting cylinders, tie-rod cylinders, welded body cylinders, and telescopic cylinders. Each type offers unique features and benefits, making them suitable for a range of industries and applications. By exploring these different types, we can gain a deeper understanding of hydraulic cylinders' versatility and adaptability.
Single Acting vs Double Acting
Single-acting cylinders exert force in one direction, typically extending or retracting the piston rod using hydraulic pressure. They are commonly used in applications where force is required in only one direction, such as pulling, lifting, or bending operations. On the other hand, double-acting cylinders provide power in both directions, enabling efficient work cycles. With double-acting cylinders, hydraulic fluid can be directed to either side of the piston, allowing for controlled movement in both directions. This makes them ideal for machinery, valve, and fittings control systems, where precise movement and versatility are paramount. Both single-acting and double-acting cylinders can be equipped with tie-rod style construction, which ensures easy cylinder maintenance, repair, and customization.
Tie Rod Cylinder
Tie rod cylinders are specifically designed to handle high-pressure hydraulic applications. They consist of a cylinder barrel, piston, piston rod, end caps, and tie rods that hold everything together. The tie rod construction allows for easy cylinder disassembly, maintenance, and repair. Tie rod cylinders often comply with industry standards such as the National Fluid Power Association (NFPA) or International Organization for Standardization (ISO) specifications, making them versatile and widely used across industries. Whether in Europe or other regions, tie rod cylinders offer reliable, durable construction and are suitable for various hydraulic applications.
Welded Body Cylinder
Welded body cylinders are designed for heavy-duty hydraulic applications, offering durability and reliability across various industries. These cylinders feature a welded construction, where the cylinder barrel and end caps are seamlessly fused together. The welded body design provides increased strength, enabling these cylinders to withstand high pressure and mechanical forces. Welded body cylinders are known for their longer lifespan compared to tie-rod cylinders, making them a preferred choice in demanding environments. Some welded body cylinders may also incorporate sensors for position feedback, allowing for precise and controlled movement. The durable construction and sensor integration make welded body cylinders suitable for critical hydraulic applications.
Telescopic Cylinder
Telescopic cylinders are unique hydraulic cylinders that use a series of nested cylinders to provide a longer stroke length without taking up much space. Often used in applications where space is limited, telescopic cylinders offer the ability to extend over a long distance while remaining compact when retracted. In construction equipment, such as cranes and excavators, telescopic cylinders allow for a long stroke length, enabling efficient movement and positioning. These cylinders are also commonly found in dump trucks and other heavy machinery, where precise control is required. When selecting a telescopic cylinder, factors such as load capacity, stroke length, and operating pressure must be carefully considered to ensure optimal performance and safety.
Key Applications of Hydraulic Cylinders
Hydraulic cylinders find extensive usage in a wide range of applications across industries. Their versatility, strength, and precise control make hydraulic cylinders indispensable in various mechanical systems. From industrial machinery and manufacturing equipment to automotive applications, hydraulic cylinders play a crucial role in powering and controlling mechanical movement. Understanding the key applications of hydraulic cylinders provides valuable insight into their significance and importance in today's industrial landscape.
Industrial Usage
Hydraulic cylinders are extensively used in industrial machinery, where precise movement and force control are crucial. Their durability, reliability, and efficient operation make them ideal for handling heavy loads and performing repetitive tasks. Some key industrial applications of hydraulic cylinders include:
- Machinery automation and control systems
- Valves and fittings for fluid control
- Construction equipment, such as excavators and bulldozers
- Material handling systems, such as conveyor belts and lifting equipment
Automotive Applications
In the automotive industry, hydraulic cylinders play a vital role in various applications, ensuring the smooth operation and control of vehicle systems. Hydraulic cylinders are commonly found in:
- Automotive lift systems, including vehicle hoists and hydraulic car lifts
- Convertible roof mechanisms, enabling seamless transformation
- Suspension systems, allowing for comfortable rides and enhanced stability
- Engine components, facilitating precise valve control and movement
Factors to Consider when Selecting a Hydraulic Cylinder
When selecting a hydraulic cylinder for a specific application, several factors need to be carefully considered to ensure optimal performance and reliability. The key factors include bore diameter, maximum stroke length, and the specifications unique to each hydraulic cylinder type. By understanding and evaluating these factors, professionals can make informed decisions and select the most suitable hydraulic cylinder for their specific requirements.
Bore Diameter
The bore diameter of a hydraulic cylinder directly affects its strength, force output, and load capacity. It determines the volume of hydraulic fluid required to move the piston, which, in turn, determines the force exerted on the load. The selection of bore diameter is influenced by the specific application requirements, including the desired force, speed, and stroke length. Greater bore diameter results in higher force capability, while smaller bore diameter cylinders are suitable for applications with lower force requirements. It is crucial to carefully consider the bore diameter when selecting a hydraulic cylinder to ensure optimal performance and safety.
Maximum Stroke Length
The stroke length of a hydraulic cylinder defines its maximum extension and retraction capabilities, directly impacting the mechanical movement it can provide. For applications requiring long stroke lengths, telescopic cylinders are often employed, as they allow for extended movement in a compact design. Consider the specific requirements of the application, including the desired range of movement and space limitations, when selecting the appropriate stroke length for hydraulic cylinders. Optimal stroke length selection ensures efficient mechanical movement, precise control, and system integrity.
Are All Hydraulic Cylinders the Same?
All hydraulic cylinders are not the same. Hydraulic cylinders vary in construction, specifications, and performance, catering to diverse industrial needs. The specific requirements of an application determine the type, size, and specifications of the hydraulic cylinder needed. Factors such as bore diameter, piston rod diameter, maximum stroke length, and valve specifications are crucial to consider when selecting a hydraulic cylinder. Each hydraulic cylinder is designed and engineered to meet specific industry standards, performance criteria, and environmental conditions. Understanding the key specifications and variations in hydraulic cylinders is essential for selecting the right cylinder for a particular application.
Conclusion
In conclusion, hydraulic cylinders play a vital role in various industries and applications. Understanding the basics of hydraulic cylinders, including their components and working mechanism, is crucial for selecting the right cylinder for your needs. Whether it's single-acting or double-acting, tie rod or welded body, or even telescopic cylinders, each type has its own advantages and applications. When selecting a hydraulic cylinder, factors such as bore diameter and maximum stroke length must be considered to ensure optimal performance. So, whether you need a hydraulic cylinder for industrial usage or automotive applications, make sure to choose wisely based on your specific requirements. Trust the power of hydraulic cylinders to deliver the force and precision you need for your projects.