Why Teflon Tape Fails in High-Pressure Systems and What Engineers Should Specify Instead
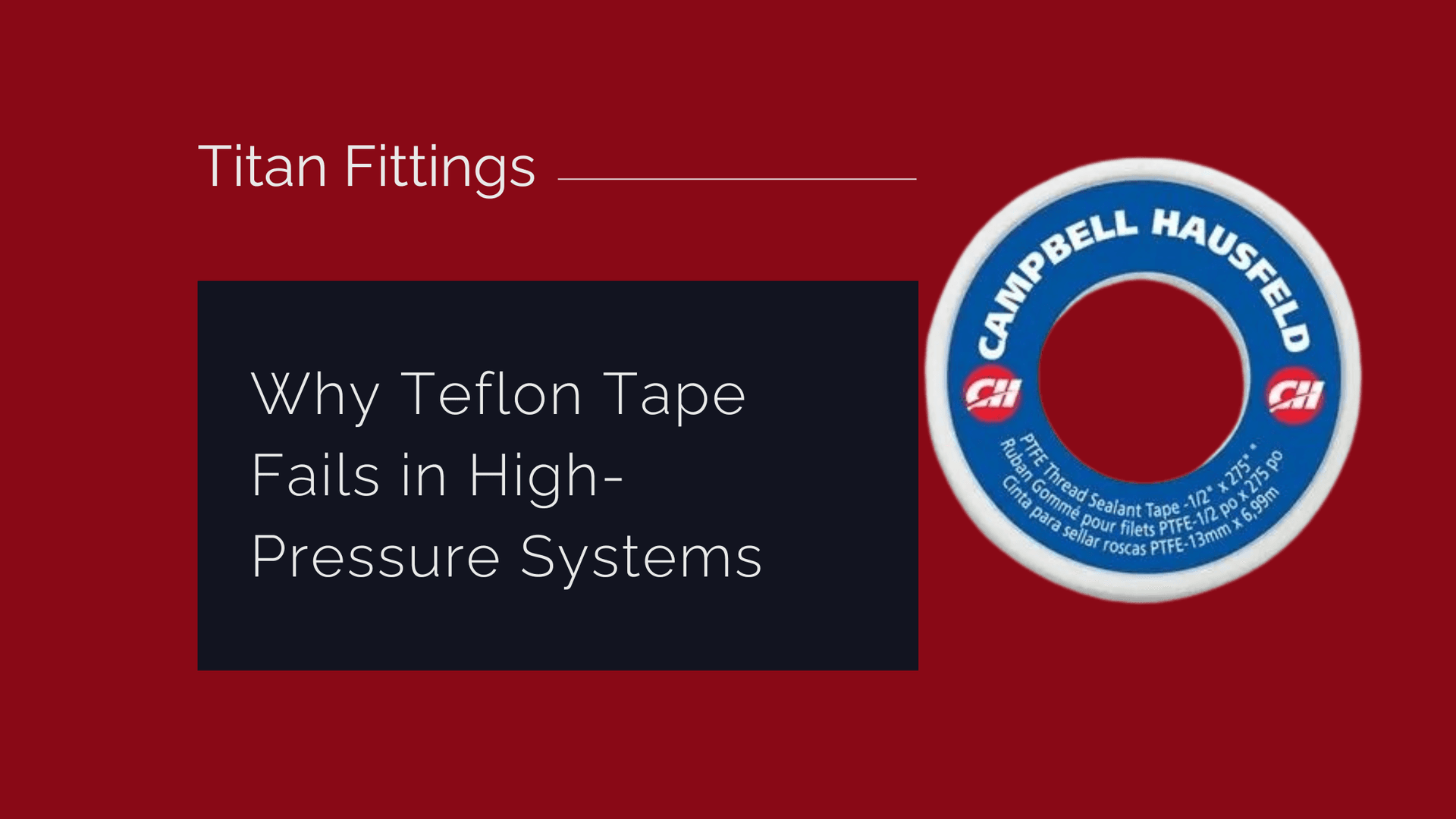
Teflon tape, also known as PTFE tape, is a common material used in plumbing and piping applications to seal threaded joints. While it is widely accepted and utilized, its effectiveness in high-pressure systems is often called into question. Understanding the limitations of Teflon tape in these environments is crucial for engineers and contractors who aim to ensure the integrity and safety of their systems.
This article delves into the reasons why Teflon tape fails in high-pressure situations and offers alternative solutions that engineers should consider when specifying sealing materials for critical applications.
One of the primary reasons Teflon tape may not perform well under high pressure is its tendency to compress and deform when subjected to extreme forces. This can lead to gaps in the seal, allowing fluids or gases to escape, which can result in leaks and potential hazards. Additionally, Teflon tape is not designed to withstand certain chemical exposures that may be present in various industrial applications, further limiting its utility. Engineers must be aware of these factors when selecting sealing materials, as the consequences of failure can be severe, ranging from minor inconveniences to catastrophic system failures.
In contrast, alternatives such as anaerobic sealants or thread sealants specifically formulated for high-pressure applications can provide a more reliable solution. These materials are designed to fill gaps and create a robust bond that can withstand the rigors of high-pressure environments. Furthermore, they often offer greater resistance to chemicals and temperature fluctuations, making them suitable for a wider range of applications. By exploring these alternatives, professionals can enhance the reliability of their plumbing systems and ensure that they meet the stringent safety standards required in today’s industrial landscape.
The Limitations of Teflon Tape
1. Compression and Seal Integrity
One of the primary reasons Teflon tape fails in high-pressure systems is its reliance on compression to form a seal. When threaded joints are tightened, the tape is compressed, which can lead to a temporary seal. However, under high pressure, the forces acting on the joint can exceed the tape's ability to maintain that seal. As pressure increases, the tape may deform or extrude from the joint, leading to leaks.
Moreover, Teflon tape is not designed to fill gaps effectively. In systems where threads may not be perfectly aligned or where there are minor imperfections, Teflon tape may not provide a reliable seal, allowing fluid or gas to escape under pressure. This is particularly critical in applications such as gas pipelines or hydraulic systems, where even a minor leak can lead to significant safety hazards or operational inefficiencies. In such cases, alternative sealing methods, such as anaerobic sealants or thread compounds, may be more suitable, as they can provide a more robust and durable seal by filling in the voids and imperfections that Teflon tape cannot address.
2. Chemical Compatibility
Another significant limitation of Teflon tape is its chemical compatibility. While PTFE is resistant to many chemicals, it is not universally compatible with all substances. In high-pressure systems, the presence of aggressive chemicals can degrade the tape, leading to failure. This degradation can occur rapidly, especially in systems that experience temperature fluctuations or exposure to corrosive substances. For instance, Teflon tape may break down in the presence of certain amines or halogenated solvents, which can compromise the integrity of the seal and lead to leaks.
Engineers must carefully consider the chemical environment in which Teflon tape will be used. In applications involving strong acids, bases, or solvents, alternative sealing materials that are chemically resistant should be specified to ensure long-term reliability. Materials such as PTFE gaskets, rubber seals, or metal sealing rings can provide better performance in harsh chemical environments, ensuring that the integrity of the system is maintained over time. Additionally, conducting compatibility tests before implementation can help identify the most suitable sealing solution for specific applications.
3. Temperature Sensitivity
Temperature variations can also affect the performance of Teflon tape. While it can withstand high temperatures, excessive heat can cause the tape to lose its mechanical properties, leading to a compromised seal. In high-pressure systems, where temperature fluctuations are common, relying solely on Teflon tape can be risky. For instance, in industrial applications involving steam or hot water, the high temperatures can cause the tape to become less effective, resulting in potential leaks that can disrupt operations and lead to costly downtime.
In addition, low temperatures can make the tape brittle, further increasing the likelihood of failure. Engineers must account for the operating temperature range of their systems and consider alternatives that offer better performance under varying thermal conditions. Materials such as silicone or fluorosilicone seals can maintain their flexibility and sealing properties across a wider temperature range, providing a more reliable solution in extreme environments. By selecting the appropriate sealing material based on temperature and pressure conditions, engineers can enhance the longevity and safety of their systems, ensuring optimal performance in demanding applications.
Alternative Sealing Solutions for High-Pressure Systems
1. Thread Sealants
One effective alternative to Teflon tape is the use of thread sealants. These products are designed to provide a more robust seal than tape by filling gaps and imperfections in threaded joints. Thread sealants, such as anaerobic adhesives, cure in the absence of air and create a solid bond that can withstand high pressures and temperatures.
These sealants are also available in various formulations to suit different applications, including those that require chemical resistance. By specifying a suitable thread sealant, engineers can enhance the reliability of their high-pressure systems significantly. Additionally, thread sealants can be beneficial in environments where vibration is a concern, as they can help maintain the integrity of the seal over time. This is particularly important in industries such as oil and gas, where equipment is frequently subjected to harsh conditions and fluctuating pressures.
2. Gasket Materials
In some cases, using gasket materials can provide a more effective sealing solution than Teflon tape. Gaskets are typically made from materials that can compress and conform to the surfaces of the mating parts, creating a tight seal. Options such as rubber, silicone, or metal gaskets can be selected based on the specific requirements of the system, including pressure, temperature, and chemical exposure.
Gaskets can be particularly beneficial in flanged connections, where the surface area is larger, and the potential for leaks is greater. By using gaskets designed for high-pressure applications, engineers can ensure a more reliable seal than what Teflon tape can offer. Moreover, the choice of gasket material can also influence the longevity of the seal; for instance, high-performance elastomers can withstand extreme temperatures and aggressive chemicals, making them ideal for demanding environments. Additionally, the use of gaskets can facilitate easier disassembly of components for maintenance, as they can often be replaced without damaging the mating surfaces.
3. Compression Fittings
Compression fittings are another viable alternative for high-pressure systems. These fittings use a mechanical compression mechanism to create a seal, eliminating the need for tape or sealants. The design of compression fittings allows for a secure connection that can withstand high pressures without the risk of leakage.
Furthermore, compression fittings can simplify installation and maintenance, as they do not require the same level of precision as threaded connections. This can be particularly advantageous in applications where quick repairs or adjustments are necessary. In addition, compression fittings are often reusable, which can lead to cost savings over time. They also come in various materials, such as brass, stainless steel, and plastic, allowing engineers to choose the best option based on the specific application and environmental conditions. This versatility makes compression fittings a popular choice in industries ranging from plumbing to aerospace, where reliability and ease of use are paramount.
Best Practices for Specifying Sealing Solutions
1. Assessing System Requirements
When specifying sealing solutions for high-pressure systems, it is essential to conduct a thorough assessment of the system's requirements. This includes evaluating the operating pressure, temperature range, and the chemical nature of the fluids or gases being transported. Understanding these factors will help engineers select the most appropriate sealing materials and methods.
Additionally, consideration should be given to the longevity and maintenance needs of the system. Choosing materials that offer durability and reliability will ultimately reduce the risk of leaks and the need for frequent repairs.
2. Consulting Material Data Sheets
Engineers should always consult material data sheets (MDS) when selecting sealing materials. These documents provide critical information about the properties and performance of materials under various conditions. By reviewing MDS, engineers can ensure that the chosen sealing solution is compatible with the specific requirements of their high-pressure systems.
Furthermore, MDS often include information on temperature limits, chemical resistance, and mechanical properties, allowing for informed decision-making that prioritizes safety and reliability.
3. Testing and Validation
Before finalizing the selection of sealing materials, it is advisable to conduct testing and validation. This may involve subjecting the materials to simulated high-pressure conditions to evaluate their performance. By performing such tests, engineers can identify any potential weaknesses or failure points in the sealing solutions before they are implemented in the field.
Testing not only helps in confirming the reliability of the chosen materials but also provides valuable data that can inform future projects and specifications.
Conclusion: Moving Beyond Teflon Tape
While Teflon tape has been a staple in plumbing and piping applications for years, its limitations in high-pressure systems cannot be overlooked. Engineers must be proactive in specifying sealing solutions that are better suited to withstand the demands of high-pressure environments. By considering alternatives such as thread sealants, gasket materials, and compression fittings, they can enhance the reliability and safety of their systems.
Ultimately, a thorough understanding of the system requirements, careful selection of materials, and rigorous testing will lead to more effective sealing solutions. By moving beyond Teflon tape, engineers can ensure that their high-pressure systems operate efficiently and safely, reducing the risk of leaks and failures.
Discover Reliable High-Pressure Solutions with Titan Fittings
Don't let the limitations of Teflon tape compromise the efficiency and safety of your high-pressure systems. At Titan Fittings, we specialize in providing superior stainless steel fittings, hose fittings, valves, and adapters that are engineered to perform under the most demanding conditions. Our products are crafted with the utmost precision, ensuring that your hydraulic systems maintain their integrity when it matters most. For both standard and custom fitting requirements, Shop Now at Titan Fittings and experience the difference that quality and durability can make in your industrial applications.