Why Hydraulic Fluid Foams And What It’s Trying to Tell You
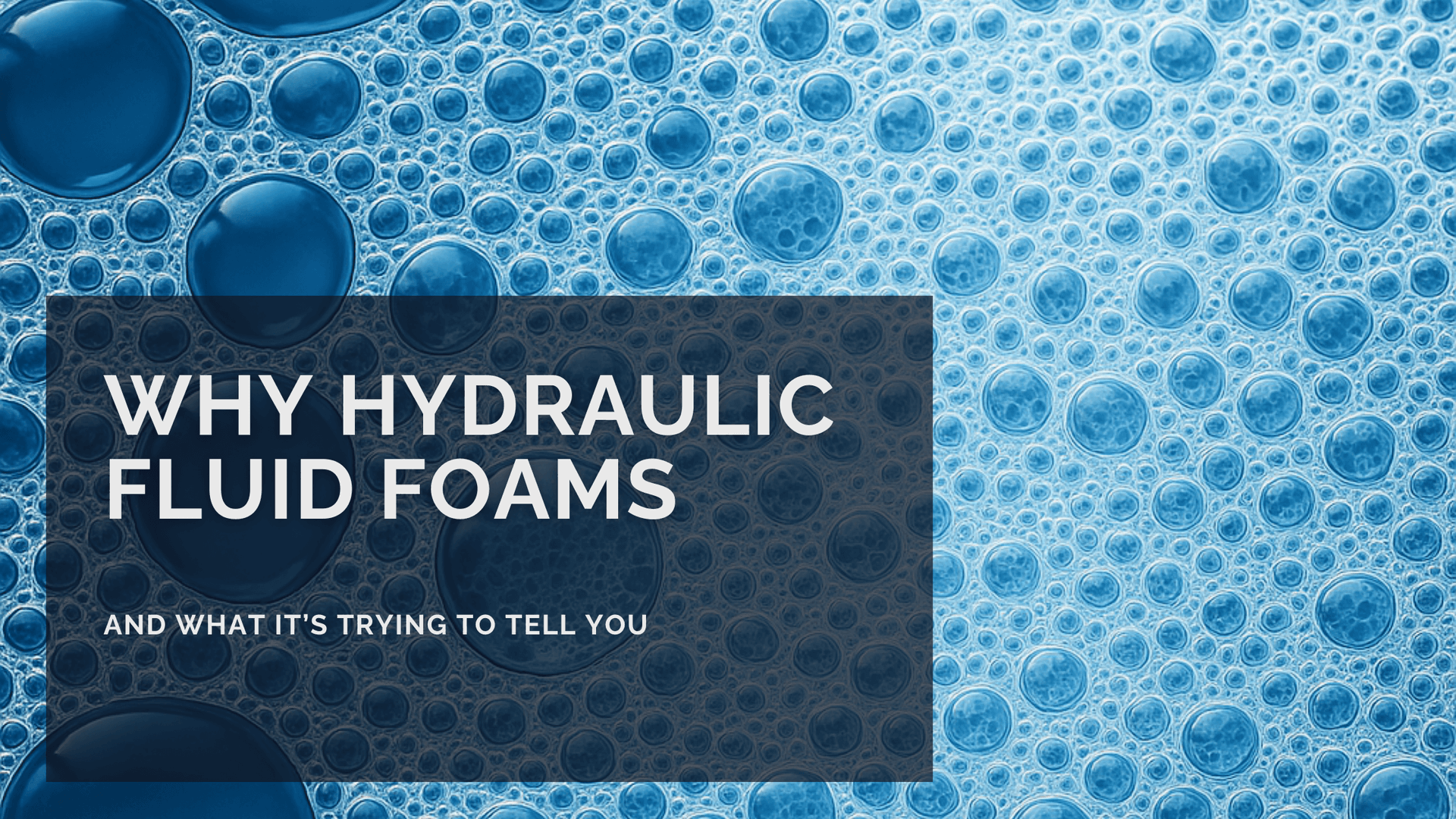
Why Hydraulic Fluid Foams And What It’s Trying to Tell You
Hydraulic systems are integral to various industries, powering machinery and equipment that rely on fluid power for operation. However, one common issue that can arise in these systems is the foaming of hydraulic fluid. Understanding why hydraulic fluid foams and what it indicates about the system's health is crucial for maintaining efficiency and preventing costly breakdowns.
Understanding Hydraulic Fluid Foaming
Foaming occurs when air is introduced into hydraulic fluid, resulting in the formation of bubbles. This phenomenon can lead to several operational issues, including reduced efficiency, increased wear on components, and even catastrophic system failures if not addressed promptly. To comprehend the implications of foaming, it is essential to explore its causes and effects.
Causes of Foaming in Hydraulic Fluids
Several factors can contribute to the foaming of hydraulic fluids. Understanding these causes can help in diagnosing the problem and implementing effective solutions.
- Air Entrapment: One of the primary causes of foaming is the entrapment of air within the hydraulic fluid. This can occur due to leaks in hoses, fittings, or seals, allowing air to mix with the fluid.
- Fluid Contamination: Contaminants such as water, dirt, or other foreign substances can alter the properties of hydraulic fluid, making it more susceptible to foaming. Water, in particular, can significantly reduce the fluid's ability to resist foaming.
- High Operating Temperatures: Elevated temperatures can lower the viscosity of hydraulic fluid, promoting air entrapment and foam formation. When fluid is heated, it can expand and create more space for air to mix in.
Effects of Foaming on Hydraulic Systems
The presence of foam in hydraulic fluid can lead to a range of negative consequences, impacting both the performance of the system and its longevity.
- Reduced Efficiency: Foaming can disrupt the smooth flow of hydraulic fluid, leading to erratic pressure and decreased system efficiency. This can result in slower response times and reduced productivity.
- Increased Wear and Tear: The presence of foam can cause cavitation, which leads to increased wear on hydraulic components. Over time, this can result in costly repairs and replacements.
- Overheating: Foaming can lead to inadequate lubrication, causing components to overheat. This can not only damage the machinery but also pose safety risks in industrial settings.
In addition to these primary effects, foaming can also interfere with the hydraulic fluid's ability to transmit power effectively. As bubbles form and collapse, they can create shock waves that lead to pressure fluctuations, further complicating the operation of hydraulic machinery. This instability can manifest as jerky movements in hydraulic actuators or inconsistent performance in hydraulic motors, which can be particularly detrimental in applications requiring precision, such as robotics or automated manufacturing processes.
Furthermore, the presence of foam can complicate maintenance procedures. When hydraulic fluid is foamy, it can be challenging to accurately gauge fluid levels, making it difficult to determine when a fluid change is necessary. This can lead to delayed maintenance and exacerbate existing issues, resulting in a vicious cycle of inefficiency and increased operational costs. Additionally, operators may find themselves frequently needing to add fluid or address leaks, diverting valuable time and resources away from other critical tasks.
Diagnosing Foaming Issues
Identifying the root cause of foaming in hydraulic fluid is essential for effective troubleshooting. A systematic approach can help pinpoint the problem and guide necessary corrective actions.
Visual Inspection
The first step in diagnosing foaming issues is conducting a thorough visual inspection of the hydraulic system. Look for signs of leaks, fluid discoloration, or contamination. Pay close attention to seals, hoses, and connections, as these are common areas where air can enter the system. Additionally, inspect the reservoir for any signs of excessive agitation or turbulence, which can exacerbate foaming. Observing the fluid's surface for bubbles or froth can also provide immediate indications of foaming problems, allowing for quicker intervention.
Fluid Analysis
Performing a fluid analysis can provide valuable insights into the condition of the hydraulic fluid. Testing for contaminants, viscosity, and moisture content can help determine whether the fluid is suitable for use or if it needs to be replaced. Regular fluid analysis can also help track changes over time, allowing for proactive maintenance. Furthermore, analyzing the presence of additives can reveal whether the fluid has degraded or lost its effectiveness, which is crucial for maintaining optimal performance. Understanding the chemical makeup of the hydraulic fluid can also assist in identifying compatibility issues with system components that might lead to foaming.
Monitoring System Performance
Keeping an eye on system performance metrics can help identify foaming issues early. Monitoring pressure levels, temperature, and response times can provide clues about the health of the hydraulic system. Any deviations from normal operating parameters should be investigated promptly. Implementing real-time monitoring systems can enhance this process, allowing for immediate alerts when performance metrics fall outside acceptable ranges. Additionally, maintaining a log of performance data can help identify patterns or recurring issues, facilitating a more comprehensive understanding of the hydraulic system's behavior over time and aiding in the development of effective maintenance strategies.
Preventing Foaming in Hydraulic Systems
Preventing foaming in hydraulic systems is far more effective than addressing it after it occurs. Implementing best practices can help maintain fluid integrity and system performance.
Regular Maintenance
Establishing a routine maintenance schedule is crucial for preventing foaming issues. Regularly check for leaks, replace worn seals, and ensure that hoses and fittings are in good condition. Additionally, changing the hydraulic fluid at recommended intervals can help maintain optimal performance. This proactive approach not only extends the life of the hydraulic components but also enhances the overall efficiency of the system. Keeping a detailed log of maintenance activities can help identify patterns or recurring issues, enabling technicians to make informed decisions about necessary adjustments or upgrades.
Use Quality Hydraulic Fluids
Choosing high-quality hydraulic fluids that are specifically formulated to resist foaming can significantly reduce the likelihood of this issue. Look for fluids that contain anti-foam additives and have been tested for performance in your specific application. Furthermore, it’s essential to consider the viscosity of the hydraulic fluid, as it can greatly influence the system's response under varying temperatures and pressures. Selecting the right viscosity grade not only improves the fluid's ability to lubricate and protect components but also minimizes the risk of aeration, which can lead to foaming.
Control Operating Conditions
Monitoring and controlling operating conditions, such as temperature and pressure, can help mitigate foaming risks. Ensure that the hydraulic system operates within the manufacturer's specified limits, and consider implementing cooling solutions if overheating is a concern. Additionally, maintaining proper fluid levels is vital; low fluid levels can introduce air into the system, exacerbating foaming issues. Using fluid level sensors or gauges can provide real-time monitoring, allowing operators to address potential problems before they escalate. Implementing these controls not only enhances the reliability of the hydraulic system but also contributes to safer operational practices.
What Foaming is Trying to Tell You
Foaming in hydraulic fluid is not just an inconvenience; it is a symptom that can reveal underlying issues within the hydraulic system. Understanding what foaming is trying to communicate can help operators take timely action. Recognizing the signs early can lead to more effective maintenance strategies, ensuring that the hydraulic system operates smoothly and efficiently.
Indication of Contamination
Foaming often indicates that the hydraulic fluid is contaminated. Whether it is due to water ingress, dirt, or other foreign particles, contamination can compromise the fluid's performance. Addressing contamination sources and ensuring proper filtration can help maintain fluid integrity. Additionally, regular testing of hydraulic fluid can identify the presence of contaminants before they escalate into more significant problems. Implementing a routine maintenance schedule that includes fluid analysis can help in early detection and prolong the life of the hydraulic components.
Signal of System Imbalance
Foaming can also signal an imbalance in the hydraulic system. This could be due to improper fluid levels, excessive heat, or malfunctioning components. Regular monitoring and adjustments can help restore balance and prevent further foaming. Moreover, understanding the operational parameters of the hydraulic system can aid in identifying the root causes of imbalance. For instance, if the system is frequently exposed to high temperatures, it may be necessary to evaluate the cooling mechanisms in place or consider using fluids with higher thermal stability to mitigate foaming issues.
Warning of Potential Failures
Ultimately, foaming can serve as a warning sign of potential failures within the hydraulic system. Ignoring this symptom can lead to more severe issues, including total system failure. Promptly addressing foaming and its underlying causes can save time, money, and resources in the long run. Furthermore, understanding the correlation between foaming and wear on hydraulic components can be crucial. Continuous foaming may lead to cavitation, which can damage pumps and valves, leading to costly repairs. Therefore, operators should not only focus on immediate fixes but also on long-term strategies to enhance system reliability and performance.
Conclusion
Hydraulic fluid foaming is a common yet significant issue that can affect the performance and longevity of hydraulic systems. By understanding the causes and effects of foaming, operators can take proactive measures to prevent it and maintain optimal system performance. Regular maintenance, quality fluid selection, and monitoring system conditions are essential strategies for mitigating foaming risks.
Ultimately, recognizing foaming as a symptom of underlying issues can lead to timely interventions, ensuring that hydraulic systems continue to operate efficiently and effectively. By addressing foaming promptly, operators can safeguard their equipment, enhance productivity, and reduce the risk of costly repairs.
Enhance Your Hydraulic System with Titan Fittings
Don't let foaming disrupt the efficiency and longevity of your hydraulic systems. At Titan Fittings, we offer a premium selection of stainless steel fittings, hose fittings, valves, and adapters that are engineered to withstand the toughest industrial demands. Ensure your hydraulic systems are equipped with the best components for optimal performance. Shop Now and find the perfect solution for your hydraulic needs.
Sources
1. Air Entrainment and Foaming in Lubricants:
-H. Wu, G. Gregory, and T. R. Thomas, "Mechanisms of Lubricant Foaming and Air Entrainment," Tribology International, vol. 40, no. 6, pp. 859-868, 2007.
-DOI: 10.1016/j.triboint.2006.08.003
2. Factors Influencing Hydraulic Oil Foaming:
-Noria Corporation, "Understanding Oil Foaming," Machinery Lubrication Magazine,
-https://www.machinerylubrication.com/Read/30896/understanding-oil-foaming
3. Impact of Foam on Hydraulic System Performance:
-B. Johnson and R. Stack, "Foaming in Hydraulic Systems: Causes, Effects, and Solutions," Hydraulics & Pneumatics, 2021.
-https://www.powermotiontech.com/pneumatics/pneumatic-valves/article/21883792/pneumatic-valve