How Fluid Viscosity Changes Under Load and Why That Matters More Than Temperature Alone
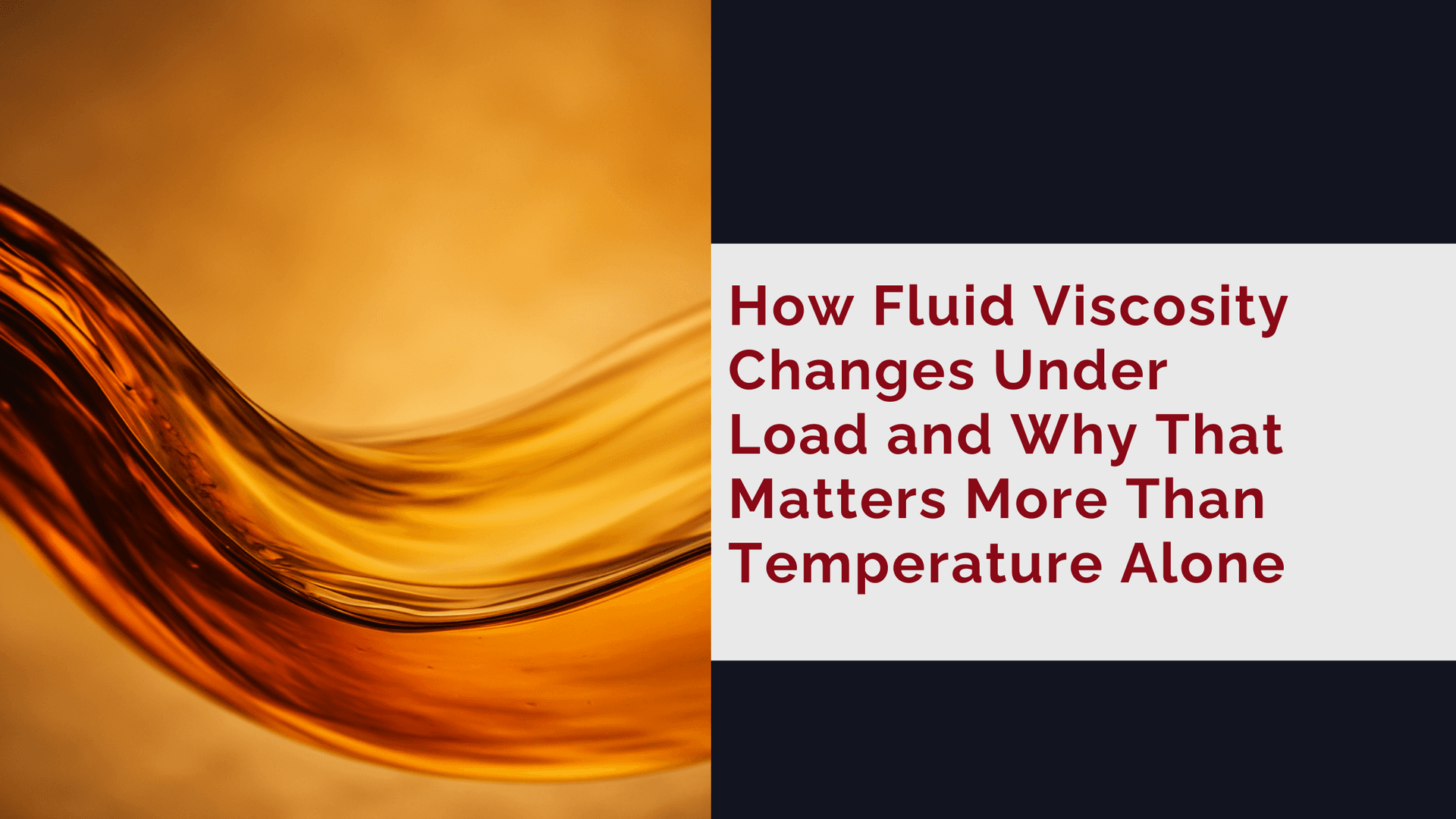
Understanding fluid viscosity is crucial in hydraulic systems, where the performance and efficiency of machinery depend significantly on the properties of the fluids used. While temperature has long been considered a primary factor affecting viscosity, the impact of load on fluid viscosity is often overlooked. This article delves into how fluid viscosity changes under load and why this aspect is critical for hydraulic systems.
The Basics of Fluid Viscosity
Viscosity is a measure of a fluid's resistance to flow. It describes how thick or thin a fluid is and is influenced by several factors, including temperature, pressure, and the nature of the fluid itself. In hydraulic systems, viscosity plays a vital role in ensuring efficient operation, as it affects the flow rates, energy losses, and overall performance of the system. For instance, a fluid with high viscosity may lead to increased energy consumption due to the extra effort required to pump it through pipes, while a fluid with low viscosity might flow too quickly, potentially causing issues such as cavitation or insufficient lubrication in moving parts.
Types of Viscosity
Viscosity can be categorized into two main types: dynamic (or absolute) viscosity and kinematic viscosity. Dynamic viscosity measures a fluid's internal resistance to flow when an external force is applied. Kinematic viscosity, on the other hand, takes into account the fluid's density and is defined as the ratio of dynamic viscosity to density. Understanding these two types is essential for engineers and technicians working with hydraulic systems, as they provide insights into how fluids behave under different conditions. For example, in applications such as lubrication, knowing the kinematic viscosity can help in selecting the right oil for machinery, ensuring optimal performance and longevity.
Factors Influencing Viscosity
While temperature is a well-known factor affecting viscosity, other elements also play a significant role. These include pressure, shear rate, and the fluid's chemical composition. As pressure increases, viscosity can change, particularly in non-Newtonian fluids, which do not have a constant viscosity. Additionally, the shear rate, or the rate at which adjacent layers of fluid move relative to each other, can alter viscosity, especially in complex fluids. For instance, certain polymers exhibit shear-thinning behavior, meaning their viscosity decreases with increasing shear rate, which can be advantageous in processes such as paint application or food processing, where easier flow is desired during mixing or pumping. Furthermore, the chemical composition of a fluid, including the presence of additives or impurities, can significantly impact its viscosity, making it crucial to monitor and control these factors in industrial applications.
The Role of Load in Viscosity Changes
Load refers to the external forces acting on a hydraulic system, which can influence the viscosity of the fluid in ways that are not immediately apparent. When a hydraulic system is under load, the behavior of the fluid can change significantly, impacting the overall performance of the system.
Understanding Load Effects
When a hydraulic system is subjected to load, the pressure within the system increases. This increase in pressure can lead to changes in the fluid's viscosity. In many cases, the viscosity of a fluid will increase under load due to the compressibility of the fluid and the interactions between fluid molecules. This phenomenon is particularly pronounced in non-Newtonian fluids, where viscosity is not constant but varies with the applied stress. For example, shear-thinning fluids will become less viscous when subjected to higher shear rates, while shear-thickening fluids will exhibit the opposite behavior. This variability necessitates a thorough understanding of the fluid characteristics in relation to the operational conditions of the hydraulic system.
Implications for Hydraulic Systems
The changes in viscosity under load can have significant implications for hydraulic systems. For instance, an increase in viscosity can lead to higher energy losses due to friction, resulting in reduced efficiency. Additionally, if the viscosity becomes too high, it can hinder the flow of the fluid, leading to potential system failures or malfunctions. Understanding these dynamics is essential for engineers and operators to optimize hydraulic system performance. Moreover, the selection of hydraulic fluids must take into account the expected operating conditions, including temperature fluctuations and varying load conditions. This ensures that the fluid maintains an optimal viscosity range, promoting effective lubrication and heat transfer within the system. Furthermore, regular monitoring of viscosity and system performance can help in early detection of issues, allowing for timely maintenance and adjustments to prevent costly downtimes.
Temperature vs. Load: A Comparative Analysis
While temperature is often the primary focus when discussing viscosity, the effects of load should not be underestimated. A comparative analysis reveals that load-induced viscosity changes can sometimes have a more significant impact on hydraulic system performance than temperature fluctuations.
The Limitations of Temperature as a Sole Factor
Temperature changes can affect viscosity, typically causing it to decrease in liquids and increase in gases. However, relying solely on temperature to predict viscosity changes can be misleading. For example, in a hydraulic system operating under varying loads, the viscosity may not respond to temperature changes in a linear manner. Instead, the load can create conditions where viscosity changes more dramatically than temperature alone would suggest.
Additionally, the interaction between temperature and load can lead to complex behaviors that are not easily predictable. As load increases, the shear stress in the fluid also rises, which can alter the fluid's molecular structure and lead to non-Newtonian behavior. This means that under high loads, the fluid may exhibit a viscosity that is not only dependent on temperature but also on the rate of shear, complicating the analysis further. Understanding these interactions is crucial for engineers and technicians who need to ensure optimal performance in hydraulic systems.
Measuring Viscosity Under Load
Accurate measurement of viscosity under load is essential for optimizing hydraulic system performance. Various methods exist for measuring viscosity, each with its advantages and limitations. Understanding these methods can help engineers select the most appropriate approach for their specific applications.
Common Viscosity Measurement Techniques
Several techniques are commonly used to measure viscosity, including rotational viscometers, capillary viscometers, and falling ball viscometers. Each method has its unique principles and is suited for different types of fluids and conditions. For instance, rotational viscometers are particularly effective for measuring viscosity under varying shear rates, making them ideal for non-Newtonian fluids.
Challenges in Measurement
Measuring viscosity under load presents several challenges. For one, the equipment must be capable of withstanding the pressures and conditions present in hydraulic systems. Additionally, ensuring accurate readings in dynamic conditions can be difficult, as viscosity may change rapidly with fluctuations in load or shear rate. Engineers must be aware of these challenges and take them into account when designing experiments or selecting measurement equipment.
Optimizing Hydraulic Systems for Viscosity Changes
To ensure optimal performance in hydraulic systems, it is essential to consider both temperature and load effects on viscosity. By understanding how these factors interact, engineers can implement strategies to mitigate adverse effects and enhance system efficiency.
Fluid Selection
Choosing the right hydraulic fluid is a critical step in optimizing system performance. Fluids with stable viscosity characteristics under varying loads and temperatures are ideal. Additionally, selecting fluids that maintain their viscosity within acceptable ranges can help prevent issues related to increased friction and energy losses.
System Design Considerations
Designing hydraulic systems with load-induced viscosity changes in mind can lead to more efficient and reliable operations. This may include incorporating features such as pressure relief valves, variable displacement pumps, and advanced control systems that can adapt to changing conditions. By anticipating viscosity changes, engineers can create systems that perform optimally under a wide range of operating conditions.
The Future of Hydraulic Systems and Viscosity Research
As technology advances, the study of fluid viscosity and its implications for hydraulic systems continues to evolve. Researchers are exploring new materials and fluid formulations that can enhance performance and reduce the impact of viscosity changes.
Innovations in Fluid Technology
Recent innovations in fluid technology have led to the development of synthetic hydraulic fluids that exhibit improved viscosity stability under varying loads and temperatures. These fluids can provide better lubrication, reduce wear, and enhance overall system efficiency. As research continues, the potential for new fluids that can further optimize hydraulic systems is promising.
Ongoing Research and Development
Ongoing research into the effects of load on viscosity is crucial for advancing hydraulic technology. By gaining a deeper understanding of how fluids behave under different conditions, engineers can develop more efficient systems and improve the reliability of hydraulic machinery. Collaborative efforts between academia and industry will play a vital role in driving these advancements.
Conclusion
In conclusion, the interplay between fluid viscosity, load, and temperature is a complex but critical aspect of hydraulic system performance. While temperature has traditionally been viewed as the primary factor influencing viscosity, the effects of load cannot be ignored. By recognizing the significance of load-induced viscosity changes, engineers can better design, maintain, and optimize hydraulic systems for improved efficiency and reliability.
As the industry continues to evolve, staying informed about the latest research and innovations will be essential for those working with hydraulic systems. By embracing a holistic approach to fluid viscosity, the potential for enhanced performance and reduced operational costs becomes increasingly attainable.
Discover the Right Fittings for Your Hydraulic Systems
Understanding the intricacies of fluid viscosity under load is just the beginning. To ensure your hydraulic systems operate at peak efficiency, you need the highest quality components. At Titan Fittings, we specialize in providing stainless steel fittings, hose fittings, valves, and adapters that are built to withstand the demands of any hydraulic environment. Our precision-manufactured products guarantee reliability and durability for all your industrial needs. Ready to enhance your hydraulic system's performance? Shop Now at Titan Fittings for superior hydraulic solutions.